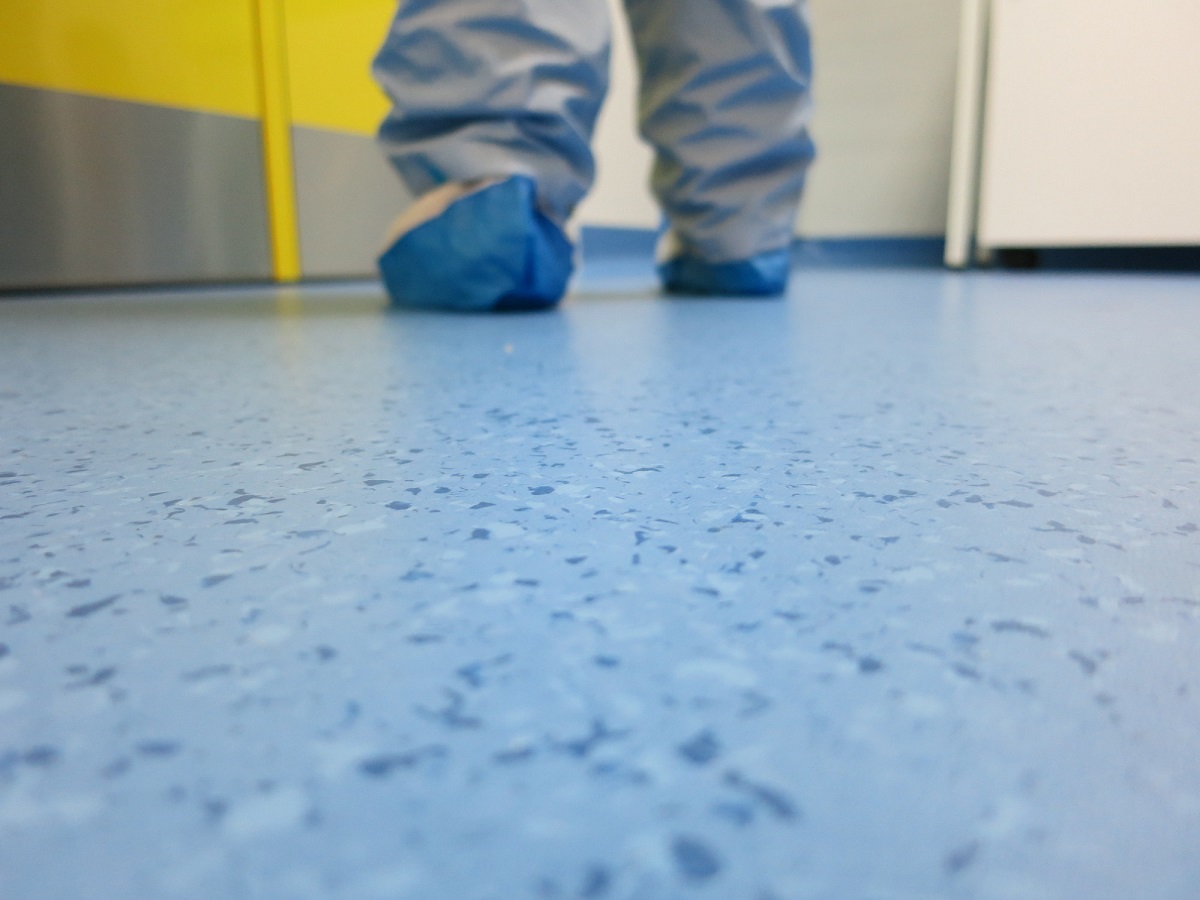
Types of Cleanroom Flooring Materials: Vinyl, Epoxy and Polyurethane
Cleanroom flooring plays a critical role in maintaining the controlled environment necessary for various industries, including pharmaceuticals, electronics, and biotechnology. Cleanrooms require flooring solutions that minimize particulate generation, are easy to clean, and are resistant to chemicals, abrasion, and microbial growth. Among the most commonly used materials for cleanroom flooring are vinyl, epoxy, and polyurethane. Each has unique properties that make it suitable for different cleanroom environments and requirements. This article will compare these materials based on several key factors: durability, cleanliness, chemical resistance, ease of installation, and cost.
Vinyl Flooring
Vinyl flooring is a popular choice for cleanrooms due to its versatility, ease of installation, and affordability. It is available in sheet form or tiles, offering flexibility in design and configuration.
Vinyl flooring is durable and can withstand moderate foot traffic. However, compared to epoxy and polyurethane, it is not as resistant to heavy machinery or frequent movement of equipment. Over time, vinyl may show signs of wear, especially in high-traffic areas.
Vinyl’s smooth surface allows for easy cleaning and disinfecting, which is essential for maintaining a sterile environment. However, the seams between vinyl tiles or sheets can become potential areas for contamination if not properly sealed, making seamless vinyl sheets a preferred option.
Vinyl flooring offers moderate chemical resistance, suitable for cleanrooms where the use of harsh chemicals is minimal. However, it may not be ideal for environments where frequent exposure to solvents or acids occurs.
Vinyl is relatively easy to install and repair, making it a cost-effective option for cleanrooms with lower contamination requirements. It can be cut and fitted around complex areas without significant difficulty.
Vinyl is generally the most affordable option, both in terms of materials and installation. Its cost-effectiveness makes it a popular choice for cleanrooms that do not require extremely stringent contamination control.
Epoxy Flooring
Epoxy flooring is a widely used cleanroom flooring material, known for its seamless finish and high durability. It is applied as a liquid and hardens into a solid, smooth surface.
Epoxy is extremely durable and can withstand heavy machinery, foot traffic, and the movement of carts and equipment. It is ideal for cleanrooms in industries such as pharmaceuticals or electronics, where durability is paramount.
The seamless nature of epoxy flooring eliminates cracks and joints where dirt, dust, and bacteria can accumulate. This makes it easy to clean and sanitize, making it ideal for cleanrooms requiring a high level of sterility.
Epoxy flooring is highly resistant to chemicals, including acids, solvents, and detergents. This makes it suitable for cleanrooms that handle hazardous materials or require frequent exposure to harsh cleaning agents.
Epoxy requires professional installation and curing time, which can take up to several days. While installation is more complex and time-consuming than vinyl, the result is a highly durable, long-lasting surface.
Epoxy is more expensive than vinyl, but its long-term durability and low maintenance costs make it a good investment for cleanrooms requiring frequent sterilization and chemical exposure.
Polyurethane Flooring
Polyurethane flooring is known for its flexibility and resilience. It is similar to epoxy in application but offers additional benefits in certain cleanroom environments.
Polyurethane flooring is exceptionally durable and resilient, particularly in environments with thermal shock or extreme temperature variations. Its flexibility allows it to absorb impacts, making it ideal for cleanrooms that experience frequent movement of heavy equipment or sudden changes in temperature.
Like epoxy, polyurethane flooring is seamless, which prevents contamination and allows for easy cleaning and maintenance. Its flexibility also ensures that cracks do not develop over time, which could compromise sterility.
Polyurethane flooring is highly resistant to chemicals, but it also offers superior resistance to organic acids, making it ideal for industries such as food and beverage processing, where both chemical and temperature resistance are required.
Similar to epoxy, polyurethane requires professional installation and curing time. While the installation process is complex, polyurethane’s resilience makes it a long-lasting solution for cleanrooms.
Polyurethane flooring tends to be the most expensive of the three materials due to its durability, chemical resistance, and ability to withstand thermal stress. However, its longevity and low maintenance needs can justify the higher initial cost.
Which Material is Right for Your Cleanroom?
- Vinyl – Excellent choice for lower-class cleanrooms or those with limited foot traffic and chemical exposure. It is cost-effective and easy to maintain.
- Epoxy – Ideal for high-class cleanrooms that require a seamless, durable, and chemical-resistant surface. Its durability and ease of cleaning make it suitable for industries such as pharmaceuticals and electronics.
- Polyurethane – Best for cleanrooms that experience extreme temperature variations or require resistance to organic acids. Its flexibility and durability make it a premium option for cleanroom environments that demand superior performance.
In summary, all three flooring materials, vinyl, epoxy, and polyurethane, have distinct advantages and are suitable for different cleanroom applications. By understanding the specific needs of the cleanroom environment, you can choose the material that will provide the best long-term performance and protection against contamination.