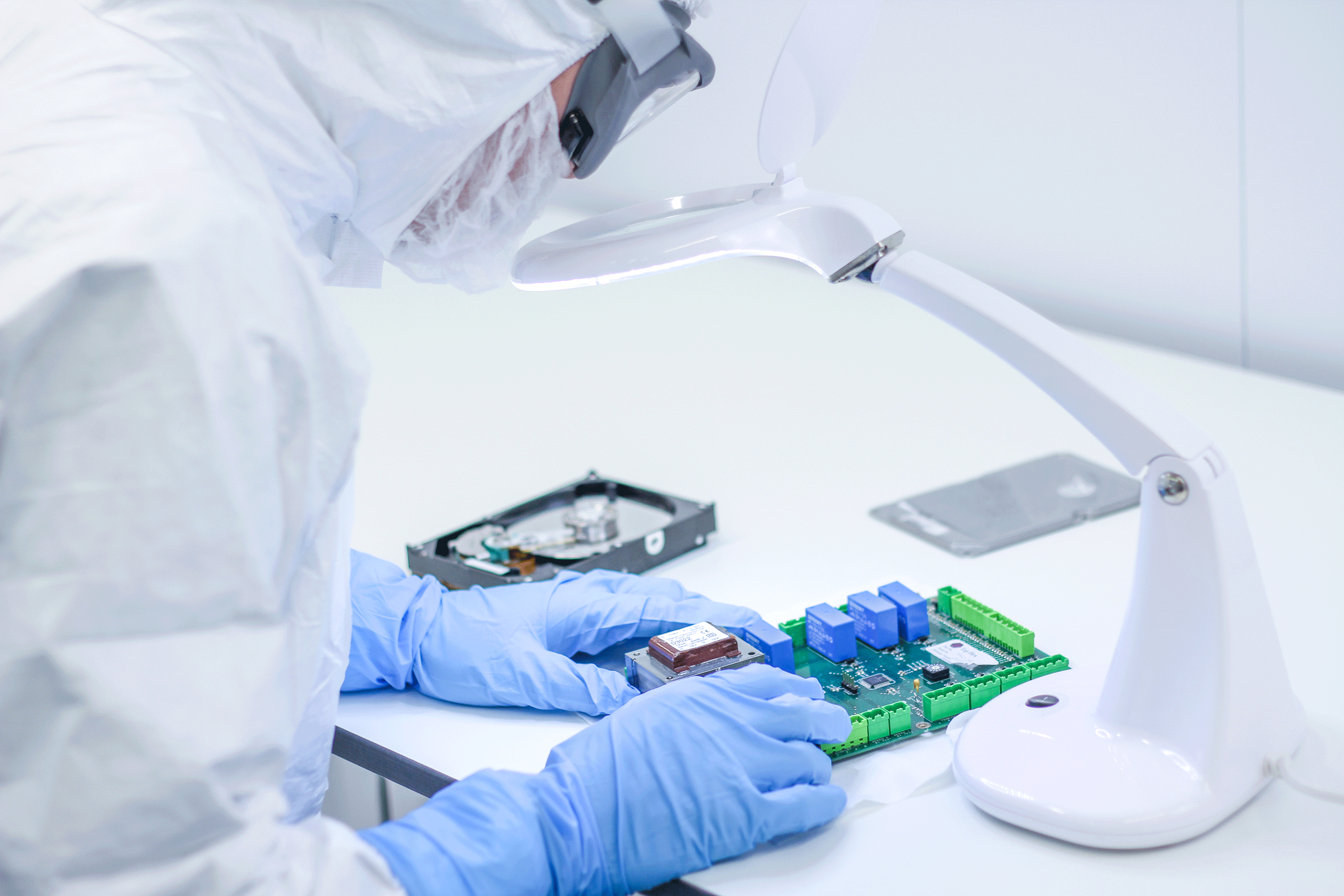
Antistatic and ESD-Safe Equipments: Why It's Critical in Cleanrooms
In cleanrooms, precision is paramount, and even the smallest disruptions can lead to significant consequences, especially in industries like semiconductor manufacturing, biotechnology, and pharmaceuticals. One of the most pervasive and often underestimated threats in these environments is static electricity, which can lead to electrostatic discharge (ESD). ESD can cause damage to sensitive components, disrupt manufacturing processes, and compromise product integrity. This makes the use of antistatic and ESD-safe equipment critical for ensuring the smooth operation of cleanrooms and safeguarding sensitive products and equipment.
The Role of ESD in Cleanrooms
Electrostatic discharge occurs when two materials with different electrical potentials come into contact and then separate, resulting in a sudden flow of electricity. In cleanrooms, ESD can generate particles and cause contamination, which contradicts the fundamental purpose of the cleanroom—maintaining a controlled environment free of contaminants.
ESD is particularly dangerous in environments where electronics and microelectronics are manufactured. For example, in semiconductor fabrication, even a tiny electrostatic discharge can destroy sensitive components or disrupt intricate processes. Furthermore, in pharmaceutical and biotech industries, ESD can lead to contamination or disruption of critical tests and experiments.
Why Antistatic and ESD-Safe Equipment is Essential
- Preventing Product Damage – Static charges can easily accumulate in cleanroom environments due to the constant movement of people and materials. Sensitive electronic components, like microchips and printed circuit boards (PCBs), can be irreversibly damaged by ESD. Using ESD-safe equipment and tools, such as ESD grounding straps, antistatic mats, and ESD-safe packaging, helps mitigate these risks, ensuring that products are not compromised.
- Maintaining Cleanroom Standards – A key aspect of cleanroom operations is maintaining a low particulate count, as even microscopic contaminants can affect product integrity. When static electricity builds up, it can attract dust and other particles to surfaces, resulting in contamination. Antistatic materials help prevent the buildup of static charge, reducing the risk of particulate attraction and contamination.
- Safeguarding Employees – ESD does not just impact sensitive products; it can also pose risks to personnel working in the cleanroom. By utilizing antistatic and ESD-safe clothing, footwear, and tools, cleanroom operators can reduce the likelihood of accidental discharges that could affect both workers and equipment.
Key ESD-Safe Equipment for Cleanrooms
To mitigate the risks of electrostatic discharge, cleanroom facilities employ a variety of ESD-safe equipment, including:
- Antistatic Workstations – These workstations are equipped with ESD mats, wrist straps, and grounding systems to ensure that static electricity is safely discharged. The surfaces are also made from antistatic materials to prevent static buildup.
- ESD-Safe Tools – Tools made from conductive materials, such as tweezers, screwdrivers, and pliers, are essential for handling sensitive components in cleanroom environments. These tools ensure that any static charge is grounded, preventing it from being transferred to the product.
- Antistatic Flooring and Footwear – Antistatic flooring materials and ESD-safe footwear, including heel straps or conductive shoes, are vital for preventing the buildup of static charges as personnel move around the cleanroom. These systems ensure that workers remain grounded and static is safely dissipated.
- Antistatic Packaging – When storing or transporting sensitive components, cleanroom operators use antistatic or ESD-safe packaging to protect products from electrostatic damage. These include bags, containers, and bubble wrap made from conductive or dissipative materials.
Conclusion
Antistatic and ESD-safe equipment play a critical role in ensuring the successful operation of cleanrooms. By preventing electrostatic discharge, cleanroom operators protect sensitive products, maintain cleanliness standards, and reduce the risk of contamination. In industries where precision and cleanliness are essential, the integration of ESD-safe tools, clothing, and workstations is not just a recommendation but a necessity for operational success.