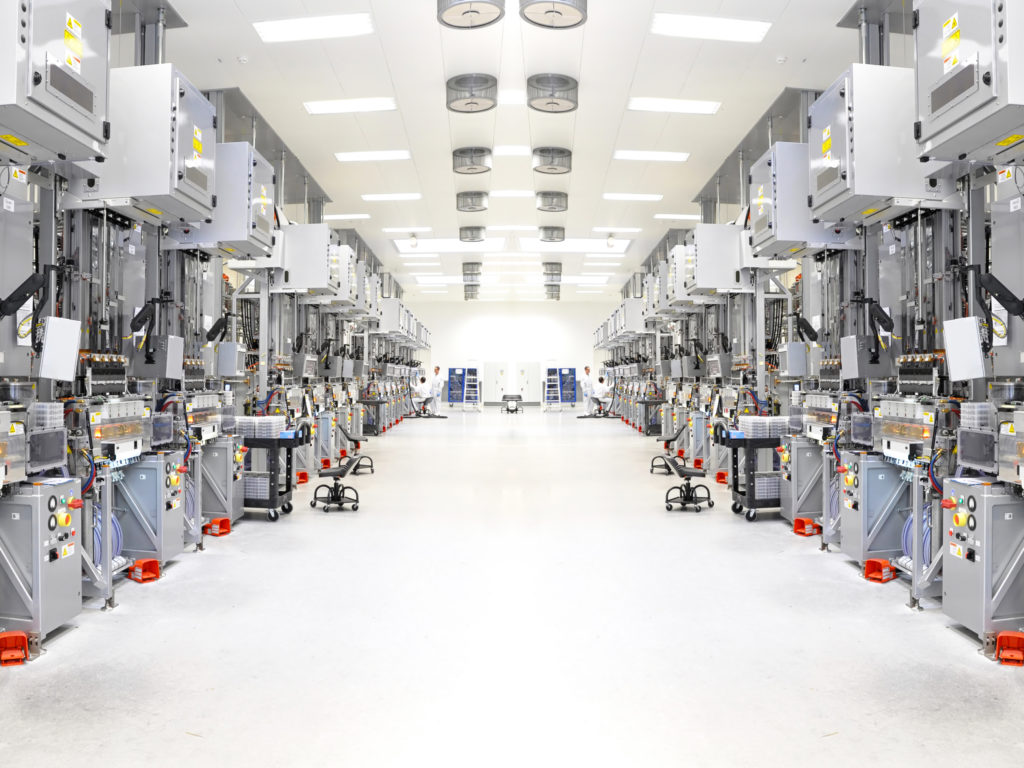
Automation in Cleanroom Maintenance
As cleanroom environments become more critical to industries like pharmaceuticals, biotechnology, semiconductors, and aerospace, maintaining the stringent standards of cleanliness and operational integrity is paramount. Traditionally, cleanroom maintenance has relied heavily on manual processes, but automation is increasingly transforming the way these environments are managed. From enhancing efficiency to reducing human error, automation plays a vital role in ensuring that cleanrooms remain compliant and operationally sound.
Enhanced Efficiency and Consistency
One of the key advantages of automation in cleanroom maintenance is the significant increase in operational efficiency. Manual maintenance processes are often time-consuming and subject to variability in human performance. Automation streamlines these tasks, ensuring they are carried out consistently and according to predefined schedules.
Robotic cleaning systems can be programmed to clean surfaces, floors, and even equipment with precision, reducing the time required for cleaning and ensuring a consistent level of cleanliness. These systems operate on regular intervals, eliminating the risk of missing critical cleaning tasks due to human error or oversight.
Automated air quality monitoring systems continuously measure particle counts, humidity, temperature, and pressure, triggering alerts if values deviate from acceptable thresholds. This allows for immediate corrective actions, preventing contamination before it escalates into a larger problem.
Minimizing Human Error
Human error is one of the most common causes of contamination and maintenance lapses in cleanrooms. From improper cleaning techniques to neglecting equipment calibration, the risk of error can compromise cleanroom integrity. Automation reduces this risk by standardizing processes that traditionally rely on human intervention.
In cleanroom environments, even minor lapses in gowning procedures can introduce contaminants. Automated gowning systems ensure personnel follow proper gowning protocols by providing step-by-step instructions and restricting access to those who do not comply with cleanliness standards.
Automated systems can schedule and monitor maintenance tasks such as filter replacement, equipment calibration, and environmental monitoring. By digitizing this process, the risk of missed or delayed maintenance tasks is eliminated, and all actions are logged for auditing purposes.
Real-Time Monitoring and Predictive Maintenance
Automation also allows for real-time monitoring of critical cleanroom conditions, enabling predictive maintenance that can prevent costly downtime and contamination events. Predictive maintenance uses data from sensors and other monitoring devices to detect early signs of equipment degradation or environmental shifts, allowing maintenance teams to address issues before they escalate.
Sensors installed in key areas of the cleanroom can continuously monitor parameters like airflow, humidity, temperature, and particle levels. Automated systems analyze the data and can initiate corrective actions when thresholds are breached.
By integrating artificial intelligence (AI) and machine learning (ML) algorithms, cleanroom systems can predict when components, such as air filters or scrubbers, will require maintenance or replacement, ensuring that parts are replaced before failures occur.
Reduced Contamination Risk
Every manual interaction within a cleanroom environment increases the risk of contamination. Automation minimizes human involvement in critical areas, reducing this risk substantially. Automated handling systems, robotic cleaning devices, and even automated product handling solutions can keep cleanrooms at optimal cleanliness levels while limiting human contact.
Automation can be integrated into material transfer systems, such as airlocks, to reduce the risk of contaminants entering the cleanroom. Automated processes eliminate the need for personnel to physically handle materials, ensuring they are transported in and out of the cleanroom without introducing particles.
Automated doors, hand sanitizing stations, and equipment can reduce the number of touchpoints in a cleanroom, further lowering the risk of contamination caused by human contact.
Compliance and Data Logging
Cleanrooms must adhere to strict regulatory standards, such as ISO 14644 or GMP (Good Manufacturing Practices), and consistent documentation is essential for proving compliance during audits. Automated systems provide real-time data logging, ensuring that all maintenance activities, environmental conditions, and corrective actions are recorded accurately and can be easily retrieved.
Automated systems log every maintenance activity, environmental reading, and alert in a centralized database. This ensures all records are accurate, tamper-proof, and readily available for regulatory inspections.
Automation ensures that every action is traceable, providing a comprehensive audit trail. Whether it’s filter changes, pressure monitoring, or environmental corrections, all activities are recorded with timestamps, making compliance audits more streamlined.
Cost Savings and Return on Investment (ROI)
While the initial investment in automation technology for cleanroom maintenance may seem high, the long-term cost savings are substantial. Automation reduces the need for manual labor, minimizes the risk of costly contamination incidents, and extends the lifespan of cleanroom equipment through predictive maintenance.
By automating routine tasks like cleaning and monitoring, businesses can reduce the need for large maintenance teams. This not only cuts labor costs but also minimizes the risk of human errors leading to contamination.
Predictive maintenance ensures that equipment is serviced before failures occur, reducing downtime and preventing costly repairs or replacements.
Conclusion
The role of automation in cleanroom maintenance cannot be overstated. It enhances efficiency, reduces contamination risks, ensures regulatory compliance, and provides significant cost savings. As cleanroom environments continue to grow in complexity, integrating automation into maintenance protocols is becoming a necessity rather than a luxury. By doing so, organizations can ensure their cleanrooms operate at peak performance while maintaining the stringent standards required in today’s highly regulated industries.