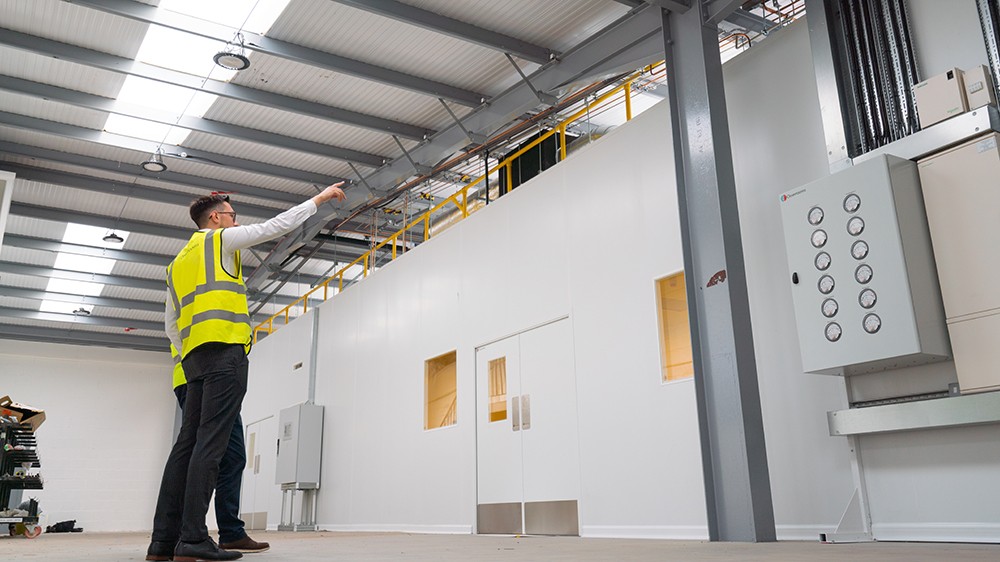
Balancing Cost and Functionality in Cleanroom Construction
Constructing a cleanroom requires a careful balance between cost and functionality. Cleanrooms are highly specialized environments designed to maintain stringent control over air quality, temperature, humidity, and other environmental factors. However, the costs associated with designing, building, and maintaining these spaces can escalate quickly. Achieving the right balance between investment and performance is crucial for long-term success.
Assess Cleanroom Requirements
It is important to establish the base foundation and requirements for a cleanroom.
ISO 14644-1 – classifies cleanrooms into nine levels, with ISO 1 being the cleanest and ISO 9 being the least clean. Each class specifies the maximum allowable number of particles (measured in microns) per cubic meter of air.
ISO 1-3 – Used for industries requiring ultra-clean environments, such as semiconductor manufacturing and nanotechnology. These cleanrooms involve the highest level of filtration and air change rates, making them the most expensive to build and operate.
ISO 4-6 – Commonly found in pharmaceutical manufacturing, biotechnology, and medical device production. These levels balance high cleanliness standards with manageable costs and maintenance needs.
ISO 7-9 – Typically used in industries like food processing or general electronics assembly, where strict contamination control is necessary but less rigorous than in pharmaceuticals or microelectronics.
Pharmaceuticals – Strict regulatory requirements (such as Good Manufacturing Practice (GMP) standards) dictate higher ISO classifications to prevent contamination that could affect product safety.
Electronics and Semiconductors – These industries demand ultra-clean environments (ISO 1–3) to prevent even microscopic particles from damaging sensitive components.
Medical Devices – Requires controlled environments (typically ISO 5–7) to ensure sterility and reduce the risk of contamination during production.
Aerospace and Optics – Dust and particles must be tightly controlled (ISO 4–6) to prevent defects in precision instruments and materials. making it fire-resistant.
Overengineering – Opting for an overly stringent ISO classification when it isn’t necessary leads to higher construction, operational, and maintenance costs. For example, constructing an ISO 4 cleanroom when an ISO 7 is sufficient would require higher-grade filtration systems, more frequent air changes, and expensive materials, all of which increase the project’s overall cost without adding meaningful benefits to operations.
Underperformance – Conversely, selecting a cleanroom class that does not meet the required standards can result in product failures, contamination issues, and even regulatory fines. In industries like pharmaceuticals or biotechnology, inadequate cleanroom performance can lead to costly recalls, product loss, and damage to a company’s reputation.
Selecting the Right Materials
Choosing the right materials can be critical for cleanrooms. Use high-quality materials in critical areas and cost-effective options in less critical zones to manage overall costs without compromising performance.
- High-End Materials – Stainless steel and epoxy coatings offer durability and superior contamination resistance but at a higher cost.
- Cost Effective Alternatives – Vinyl flooring and modular walls are less expensive but may require more frequent replacement or maintenance.
Prioritize Energy Efficiency
Prioritize efficiency of energy that help can reduce operational costs.
- Energy-Efficient Options – Variable air volume (VAV) systems, energy-efficient HEPA filters, and LED lighting.
- Cost Impact – While the initial setup is higher, long-term savings in energy and operating expenses justify the investment.
- Sustainability – Energy-efficient systems also align with environmental goals and reduce operational costs over time.
Integrate Automation and Smart Systems
Automation increases compliance with regulatory standards, reducing the risk of costly violations.
- Automation – Systems for airflow management, real-time monitoring, and access control can minimize contamination and reduce manual intervention.
- Smart Technology – Though the upfront cost is higher, long-term operational savings through reduced labor and error rates make it worthwhile.
Conclusion
Balancing cost and functionality in cleanroom construction is a strategic process that requires careful planning, informed decision-making, and a clear understanding of operational needs. By optimizing the design, choosing appropriate materials, and integrating energy-efficient and automated systems, businesses can build cleanrooms that meet industry standards while keeping costs manageable. The right approach ensures a high-performance environment that supports long-term operational success without unnecessary financial strain.