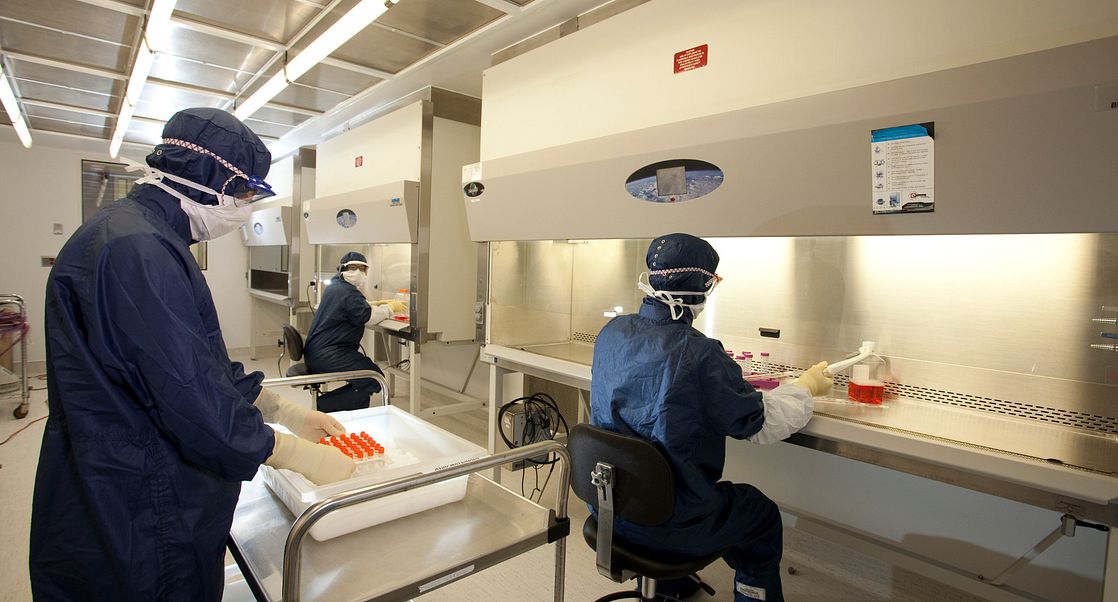
Common Cleanroom Maintenance Mistakes and How to Avoid Them
Cleanroom maintenance is crucial for ensuring optimal performance and preventing contamination, but even minor oversights can compromise the controlled environment and lead to operational inefficiencies. Below are some common cleanroom maintenance mistakes and strategies to avoid them, helping to maintain the integrity and functionality of these specialized spaces.
Neglecting Regular Filter Replacement
Cleanroom filters, such as HEPA and ULPA, are the first line of defense against airborne particles. Over time, filters become clogged with contaminants, reducing airflow and increasing the risk of particle infiltration.
Avoidance Tips:
- Establish a strict replacement schedule based on manufacturer recommendations and operational demands.
- Conduct regular airflow tests to ensure filters are functioning optimally.
- Maintain a stock of replacement filters to avoid delays.
Improper Cleaning Techniques
Using incorrect cleaning solutions or techniques can lead to surface contamination or degradation of cleanroom materials. Inadequate cleaning procedures may also leave residues that accumulate over time, compromising air quality.
Avoidance Tips:
- Use only approved cleaning agents that are compatible with cleanroom materials.
- Follow a detailed cleaning protocol, including the appropriate wiping techniques to reduce particle dispersion.
- Train cleaning staff on industry-specific best practices to ensure thoroughness.
Inconsistent Documentation
Failing to log maintenance activities can lead to missed steps, such as skipping filter changes or missing equipment calibration deadlines. This oversight can result in non-compliance with ISO standards.
Avoidance Tips:
- Implement a centralized digital system for documenting all maintenance activities, including cleaning schedules, filter replacements, and equipment calibrations.
- Regularly audit these records to ensure compliance and identify areas for improvement.
Overlooking Equipment Calibration
Cleanroom equipment, such as particle counters, pressure gauges, and temperature sensors, requires regular calibration to ensure accuracy. Ignoring calibration schedules can lead to inaccurate readings, compromising the environment.
Avoidance Tips:
- Create a routine calibration schedule and adhere to it strictly.
- Outsource calibration to certified professionals when necessary to ensure accuracy.
Inadequate Staff Training
One of the most significant risks to cleanroom maintenance is human error. Improper handling of equipment, incorrect cleaning techniques, or failure to follow gowning protocols can introduce contaminants.
Avoidance Tips:
- Provide continuous training to staff on the latest cleanroom procedures, gowning protocols, and cleaning methods.
- Implement refresher courses and periodic testing to ensure compliance.
Ignoring Wear and Tear on Surfaces
Cleanroom surfaces such as floors, walls, and ceilings undergo wear and tear over time. Scratches or cracks can harbor contaminants, compromising the sterile environment.
Avoidance Tips:
- Conduct routine inspections of all surfaces and materials within the cleanroom.
- Replace or repair any damaged surfaces immediately to prevent contamination.
Failing to Monitor Environmental Conditions
Temperature, humidity, and pressure differentials are critical factors in maintaining cleanroom standards. Failing to monitor these conditions in real-time can lead to fluctuations that compromise the environment.
Avoidance Tips:
- Install automated monitoring systems that provide real-time data on environmental conditions.
- Set alerts for deviations from acceptable ranges and implement corrective actions immediately.
Ignoring High-Traffic Areas
High-traffic areas, such as entry points and corridors, are more susceptible to contamination due to the constant movement of personnel and materials. These areas often require more frequent cleaning and monitoring.
Avoidance Tips:
- Identify high-traffic zones and increase the cleaning frequency in these areas.
- Use airlocks and separate changing areas to minimize particle transfer from outside environments.
Infrequent Preventive Maintenance
Some cleanroom operators only perform maintenance when issues arise, rather than adopting a proactive approach. Reactive maintenance can lead to equipment failures or contamination issues that could have been prevented.
Avoidance Tips:
- Implement a preventive maintenance plan that includes scheduled inspections, cleaning, and equipment servicing.
- Regularly update the plan based on the condition of the facility and equipment performance data.
Conclusion
Maintaining a cleanroom requires consistent attention to detail and a proactive approach to prevent issues before they arise. By avoiding these common mistakes, cleanroom operators can ensure optimal performance, prolong equipment life, and maintain compliance with industry standards. With the right protocols in place, a cleanroom can function as intended, safeguarding product integrity and operational efficiency.