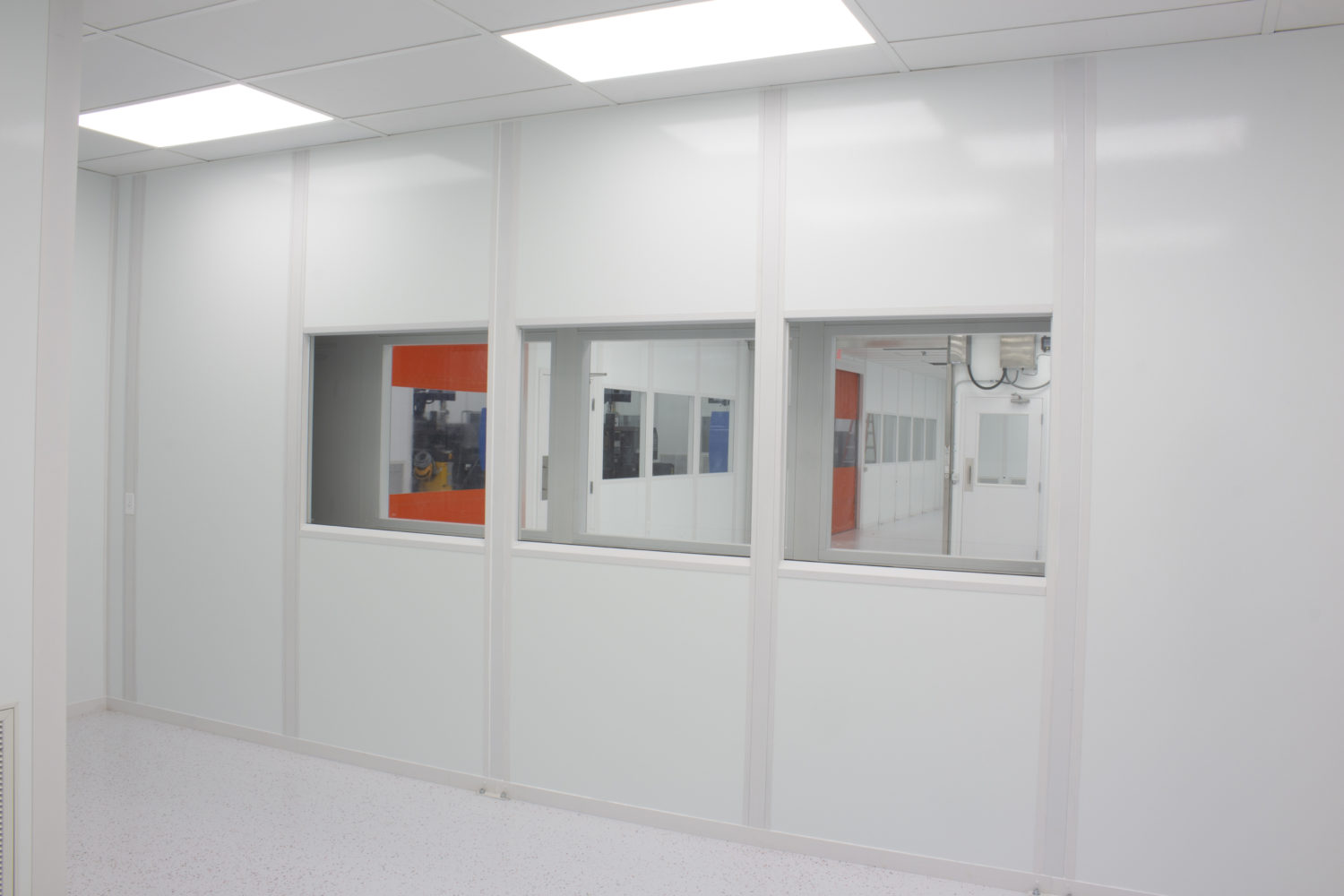
Types of Cleanroom Wall Materials: Stainless Steel, Aluminium, PVC, and FRP
Selecting the right wall material is crucial for maintaining a cleanroom’s stringent environmental controls. Let’s explore four key options (stainless steel, aluminium, PVC, and FRP) and understand their unique properties, advantages, and disadvantages. Whether you need durability, cost-effectiveness, or specific chemical resistance, this overview will help you make an informed choice for your cleanroom’s needs.
Stainless Steel
Stainless steel is a robust and highly reliable material often used in high-grade cleanrooms due to its durability, cleanliness, and resistance to contamination.
Corrosion Resistant – Stainless steel has excellent resistance to rust and corrosion, especially in environments where humidity or frequent cleaning with harsh chemicals is required.
Non-Porous Surface – The smooth, non-porous surface of stainless steel ensures that contaminants such as particles, bacteria, and other microbes cannot penetrate or accumulate on the surface.
Durability – Stainless steel is extremely tough, able to withstand impacts, high temperatures, and frequent cleaning with minimal wear or damage.
Aesthetic Appeal – It has a clean, professional look and retains its appearance over time, making it ideal for environments where visual cleanliness is important.
Long-Term Durability – Stainless steel can last for decades without significant wear or damage, even under extreme conditions.
High Chemical Resistance – Stainless steel can withstand exposure to disinfectants, acids, solvents, and sterilizing agents without degradation.
Easy Maintenance – Stainless steel is easy to clean and maintain, requiring only regular wiping down with disinfectants.
Fire Resistance – Stainless steel is non-combustible and has a high melting point, making it fire-resistant.
Cost – Stainless steel is one of the most expensive materials used in cleanrooms, both in terms of material cost and installation.
Weight – Stainless steel is heavy, making it more difficult to install than lighter materials like aluminium or PVC. This may also lead to higher labour costs during installation.
Reflection/Glare – Its shiny surface may cause glare under certain lighting conditions, which can be an issue in environments requiring precise visual work.
Aluminium
Aluminium is a lightweight, yet strong material commonly used for cleanroom walls, particularly in modular cleanrooms or environments that may require frequent reconfiguration.
Corrosion Resistant – Aluminium forms a natural oxide layer that protects it from corrosion. Coating it can further enhance its resistance to environmental factors.
Lightweight – Aluminium is much lighter than stainless steel, making it easier to transport, install, and reconfigure.
Thermal Conductivity – Aluminium conducts heat efficiently, which can be advantageous in temperature-sensitive environments.
Strength-to-Weight Ratio – While lightweight, aluminium still provides strong structural support and can withstand moderate impacts.
Cost-Effective – Aluminium is less expensive than stainless steel, providing a good balance between performance and affordability.
Easy Installation – Due to its light weight, aluminium panels are easier and faster to install, which can reduce labour costs.
Versatile – Aluminium can be anodized, powder-coated, or treated to meet various aesthetic and functional requirements (e.g., antimicrobial coatings).
Corrosion Resistant – When properly treated, aluminium can resist corrosion even in high-humidity or mildly acidic environments.
Less Durable than Steel – Aluminium is softer and more prone to scratching, denting, and wear over time, particularly in high-traffic areas.
Requires Coatings for Specific Applications – Aluminium by itself is not as resistant to chemicals as stainless steel, so additional coatings may be needed in environments exposed to harsh substances.
Conducts Electricity – In some applications, aluminium’s electrical conductivity may pose a risk, requiring additional insulation or protective measures.
PVC (Polyvinyl Chloride)
PVC is a plastic-based material that is often used in cleanroom environments where flexibility, cost-effectiveness, and ease of maintenance are key.
Lightweight – PVC is much lighter than both stainless steel and aluminium, making it easy to handle and install.
Non-Porous – The surface of PVC is smooth and non-porous, preventing contaminants from penetrating the surface and making it easy to clean.
Chemical Resistance – PVC is highly resistant to most chemicals, including acids, alkalis, and cleaning agents.
Fire Retardant – Certain grades of PVC are fire-resistant, making them safer in environments where flammability is a concern.
Affordable – PVC is significantly cheaper than metal materials like aluminium or stainless steel, making it ideal for budget-conscious projects.
Easy Installation and Customization – PVC panels are easy to cut, shape, and install, allowing for quick setup and flexibility in design.
Chemical Resistance – Resistant to most chemicals and cleaning agents, making it ideal for environments where frequent cleaning is required.
Moisture Resistant – PVC is not affected by humidity, so it won’t warp, rot, or degrade in wet environments.
Limited Durability – PVC is less durable than stainless steel and aluminum, especially in high-traffic areas or environments with heavy equipment. It is prone to scratching, cracking, and wear over time.
Temperature Sensitivity – PVC is less tolerant of extreme temperatures, and it may degrade or warp under high heat.
Environmental Concerns – PVC production and disposal are linked to environmental concerns due to the release of harmful chemicals.
FRP (Fiberglass Reinforced Panels)
FRP are composite materials made from fiberglass embedded in a resin matrix, providing high durability and resistance to impact, moisture, and chemicals.
High Impact Resistance – FRP is tough and resistant to impact, making it ideal for environments where walls might be subject to physical wear and tear.
Moisture and Mould Resistant – FRP is highly resistant to moisture, mould, and mildew, making it ideal for wet or humid environments.
Chemical Resistance – FRP panels can withstand exposure to a wide range of chemicals, including harsh solvents and acids.
Low Maintenance – FRP is easy to clean and maintain, with surfaces that resist staining and are highly durable.
Durability – FRP panels are resistant to impact, chemicals, and moisture, making them one of the most durable options for cleanroom walls.
Cost-Effective – FRP is more affordable than stainless steel and can be a good option for environments requiring durability but with a lower budget.
Moisture Resistant – Perfect for areas where walls might be exposed to water or other liquids.
Fire Resistant – Some grades of FRP are fire-resistant, making them suitable for environments where fire safety is a concern.
UV Degradation – Over time, FRP may degrade if exposed to direct sunlight, causing discoloration and weakening of the material.
Limited Customization – FRP have fewer options for customization in terms of finishes, colours, or textures compared to materials like PVC or aluminium.
Aesthetics – FRP are more functional than aesthetically pleasing, and their industrial appearance may not be suitable for environments where visual appeal is important.
Which Material is Right for Your Cleanroom?
- Stainless Steel – Best option for high-grade cleanrooms requiring sterility, chemical resistance, and durability but comes with a high cost.
- Aluminium – A lightweight, corrosion-resistant solution suitable for modular cleanrooms and environments needing flexibility but is less durable than stainless steel.
- PVC – Cost-effective and easy to install, making it ideal for lower-class cleanrooms and environments where contamination control is important but not critical.
- FRP – Combines durability and resistance to moisture and chemicals, making it perfect for environments with heavy use and exposure to harsh conditions, though it may lack the aesthetics or flexibility of other materials.