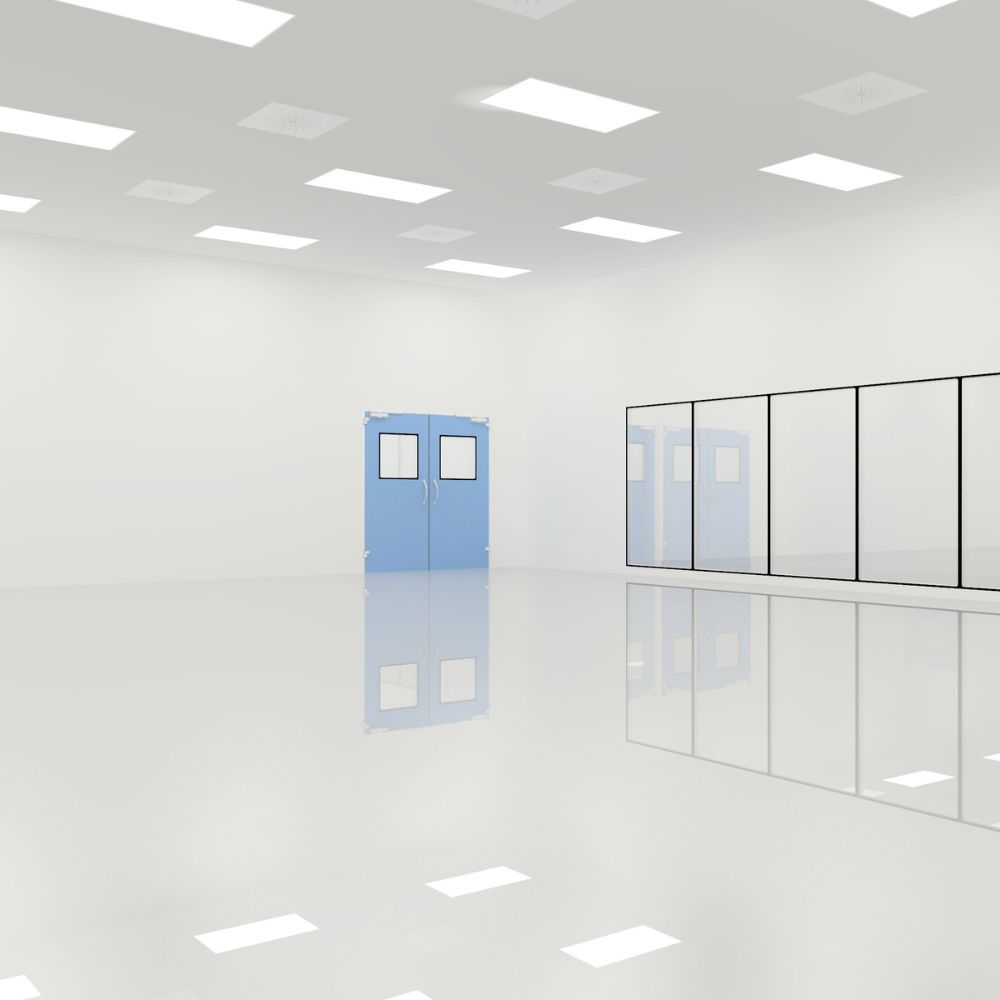
Essential Steps for Building a Cleanroom
Building a cleanroom involves careful planning, design, and construction to create a controlled environment that minimizes particle contamination. Here are some essential steps for building a cleanroom.
Evaluate Layout for People/Material Flow
Start by considering how people and materials will move within your cleanroom and optimize the layout to minimize cross-contamination and ensure efficient workflows. Determine and decide the best arrangement of workstations, equipment, and storage areas.
Determine Cleanroom Classification
Understand the cleanliness levels required for your operations. Cleanrooms are classified based on ISO standards. Choose the appropriate cleanliness level (ISO 1 to ISO 9) based on your application. Factors like particle count, air change rates, and filtration efficiency influence the classification. The higher the cleanliness class, the more precise the environmental controls.
Material Selection
The materials used in constructing a cleanroom must be selected based on ease of cleaning, resistance to chemicals, and the ability to prevent particle shedding.
- Walls and Ceilings – Should be made from materials like stainless steel, glass, epoxy-coated panels, or modular systems that are non-porous and easy to clean. Ceiling considerations may also include the need for integrated lighting, air diffusers, and access panels.
- Doors and Windows – Should be airtight, made from smooth, non-shedding materials. Windows may be double-paned with sealed edges to minimize contamination.
- Floors – Should be smooth, easy to clean, and resistant to chemicals. Epoxy or vinyl flooring is common.
Design HVAC Systems
Heating, ventilation, and air conditioning (HVAC) systems play a crucial role. Effective cleanroom design relies on managing airflow to maintain air purity. This includes using HEPA or ULPA filters to remove airborne contaminants. The type of airflow (laminar or turbulent) depends on the required cleanliness. Laminar airflow is best for high-precision environments like semiconductor manufacturing, while turbulent airflow can be used in less critical cleanrooms.
Determine Space Air Balance
Achieve proper air balance to prevent contaminants from entering the cleanroom. Positive pressure keeps contaminants out by pushing air outward when doors are opened, ideal for environments like electronics manufacturing. Negative pressure, on the other hand, prevents hazardous materials from escaping into surrounding areas, crucial in labs dealing with dangerous substances.
Plan for Utilities and Services
Consider electrical outlets, lighting, plumbing, and gas lines. Ensure they meet cleanroom requirements and allocate space for utility rooms (mechanical, electrical, and storage).
Construction and Start-Up
Work with experienced contractors who understand cleanroom specifications and verify that the cleanroom meets design requirements during start-up and commissioning.
Remember, cleanroom design is critical for industries like electronics, pharmaceuticals, and biotech, where even small particles can impact product quality. By following these steps, you’ll create an efficient and contamination-controlled environment.
Some useful resources for more information: