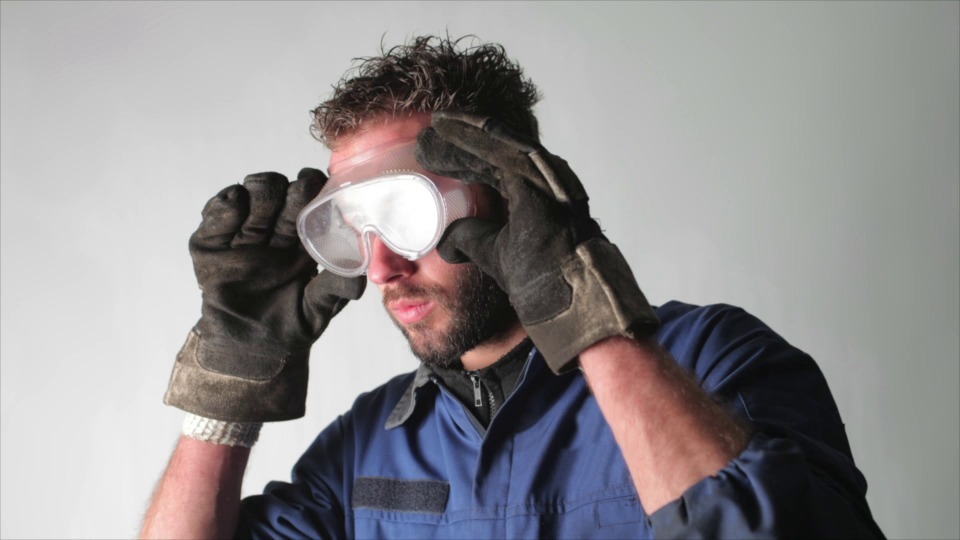
Eye Protection for Cleanroom Safety
In cleanroom environments, maintaining sterility and minimizing contamination is paramount. While much attention is given to respiratory and overall body protection, eye protection plays an equally crucial role in both safeguarding workers and preserving the cleanliness of the space. However, a common challenge is balancing comfort with the level of protection needed to ensure safety and prevent contamination.
Importance of Eye Protection in Cleanrooms
Eye protection is necessary in cleanrooms for several reasons:
Human eyes can be a significant source of contamination in cleanrooms. Particles from tears, eyelashes, and skin around the eyes can enter the cleanroom environment, which could compromise sterile operations, especially in industries like pharmaceuticals or microelectronics.
Many cleanroom operations involve hazardous chemicals or fine particles that can irritate or damage the eyes. Proper eye protection shields workers from these harmful substances, including splashes, vapors, or exposure to UV light.
In cleanrooms where machinery or equipment is used, the risk of mechanical eye injuries from flying debris, dust, or fragments is also a concern. Eye protection helps prevent these potential injuries.
Types of Eye Protection in Cleanrooms
Choosing the right eye protection depends on the specific requirements of the cleanroom environment, including the level of contamination control and the type of risks present.
Safety glasses are typically the most common form of eye protection in cleanrooms. They shield the eyes from particulates and chemical splashes. They should be designed to minimize particle shedding and be easy to clean, maintaining the sterile conditions of the cleanroom.
In environments with higher risk, such as those involving toxic chemicals or potential splash hazards, goggles provide a more secure fit around the eyes. They offer better sealing and are designed to prevent any particles or harmful substances from reaching the eyes.
For environments where workers face risks from chemical splashes or vapor exposure, face shields provide full-face protection. This can be especially useful in industries that involve high-risk chemical handling or cleaning processes.
Balancing Comfort and Safety
The primary challenge in selecting eye protection for cleanrooms is ensuring a balance between comfort and safety. Uncomfortable protective eyewear can lead to decreased compliance among workers, increasing the risk of contamination and injury. Here are several key considerations for achieving this balance:
- Ergonomics and Fit – Ill-fitting or heavy eye protection can cause discomfort, pressure points, or fatigue over long periods of wear. Opting for ergonomically designed eyewear with adjustable features can improve comfort without compromising safety.
- Anti-Fog and Ventilation Features – Cleanrooms often have high levels of humidity, which can cause goggles and glasses to fog, impairing vision and causing distractions. Anti-fog coatings and adequate ventilation systems in eyewear help prevent fogging and maintain clear vision.
- Lightweight Materials – Protective eyewear made from lightweight, durable materials such as polycarbonate or polyethylene helps reduce strain on the wearer. These materials also offer strong protection against impacts and chemical splashes.
- Sterility and Cleanability – Eye protection in cleanrooms must be easy to clean and sterilize without degradation. Reusable eyewear should be designed to withstand frequent cleaning with sterilizing agents, while disposable options should meet the necessary cleanliness standards for the specific class of cleanroom.
Conclusion
Eye protection in cleanrooms is essential for maintaining safety and cleanliness. Striking the right balance between comfort and protection ensures that workers are safeguarded from hazards while also contributing to the sterile environment. By selecting the appropriate eye protection based on the specific risks present, and ensuring proper fit and comfort, cleanroom operations can remain safe, efficient, and compliant with industry standards.