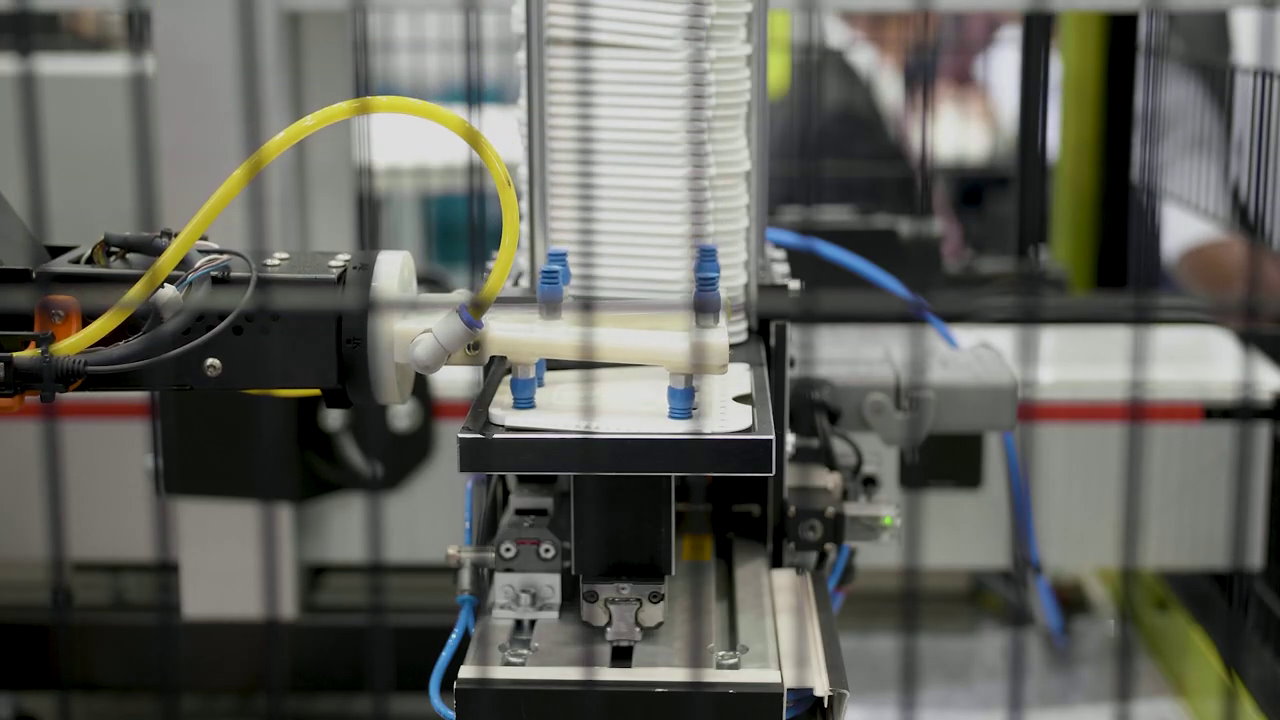
Fused Filament Fabrication (FFF) in Cleanrooms
The role of Fused Filament Fabrication (FFF) in cleanroom applications is becoming increasingly significant as industries seek to leverage 3D printing technology for customized, cost-effective solutions while adhering to stringent cleanliness standards. This article explores the advantages and challenges of using FFF in cleanroom environments, particularly in sectors like semiconductor manufacturing and pharmaceuticals.
Advantages of FFF in Cleanroom Applications
One of the primary benefits of FFF technology is its cost efficiency. Compared to traditional manufacturing methods, 3D printing can reduce the capital costs of producing labware and equipment by up to 90-99%. This is particularly advantageous in cleanrooms where specialized tools are often prohibitively expensive.
FFF allows for rapid prototyping and customization of lab equipment tailored to specific applications. This flexibility enables researchers to design and produce unique components, such as wafer storage boxes and positioning tools, that meet precise requirements without the need for expensive tooling. The ability to quickly iterate designs enhances product development cycles, allowing for faster experimentation and innovation.
FFF technology supports a wide range of materials, including common plastics like PLA and ABS, as well as advanced composites. This diversity enables the production of parts that can withstand the chemical environments typically found in cleanrooms. Recent studies have shown that 3D printed components made from PLA and ABS can generate particle levels comparable to commercial equivalents, making them viable options for cleanroom use.
The speed at which FFF can produce parts significantly shortens lead times from design to production. This rapid turnaround is crucial in fast-paced research environments where time-sensitive experiments are common. The ability to print on-demand minimizes delays associated with sourcing traditional components.
Challenges Facing FFF in Cleanroom Environments
Despite its advantages, the use of FFF in cleanrooms raises concerns about contamination. The process of 3D printing can generate particles that may compromise cleanliness standards. Research indicates that particle generation during fabrication depends on various factors, including filament type, color, and printing parameters. Therefore, careful selection of materials and adherence to best practices are essential to mitigate these risks.
While many materials are suitable for FFF, not all are appropriate for cleanroom applications. The choice of filament must consider factors such as chemical compatibility and particle generation potential. Studies have highlighted that natural-colored filaments should be preferred to avoid metal contamination from colorants, especially in sensitive applications like semiconductor processing.
Compliance with ISO standards is critical in cleanroom settings. The introduction of new materials or processes requires extensive testing to ensure they meet cleanliness requirements. Ongoing research is necessary to validate the performance of 3D printed components under controlled conditions.
The surface finish of FFF parts can also pose challenges; layer lines from the printing process may trap contaminants, complicating cleaning efforts. Post-processing techniques may be required to achieve a smooth finish suitable for cleanroom environments.
Conclusion
Fused Filament Fabrication presents a promising avenue for enhancing cleanroom operations through cost-effective customization and rapid prototyping. While there are challenges related to contamination risks, material limitations, regulatory compliance, and surface finish quality, ongoing research continues to demonstrate the viability of 3D printed components in controlled environments. As industries increasingly adopt FFF technology, it is essential to address these challenges proactively to fully harness its potential in cleanroom applications. By doing so, organizations can improve efficiency while maintaining the high standards required for sensitive processes.