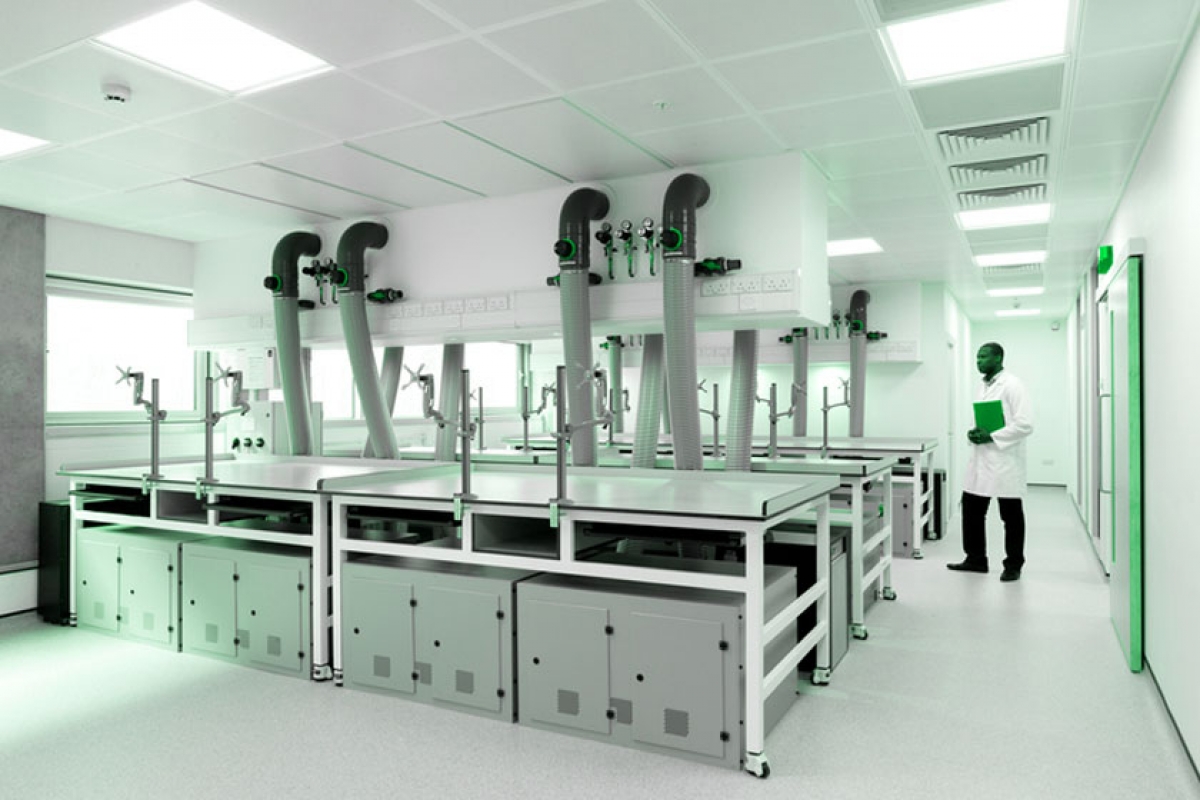
Introduction to Cleanroom HVAC Systems
Heating, Ventilation, and Air Conditioning (HVAC) systems play a critical role in the functionality and effectiveness of cleanrooms across industries like pharmaceuticals, biotechnology, electronics, and healthcare. Cleanrooms are highly controlled environments designed to minimize contamination, and the HVAC system is integral in maintaining strict control over air quality, temperature, humidity, and pressure.
The Role of HVAC Systems in Cleanrooms
An HVAC system in a cleanroom is not just about heating or cooling; it must also filter and circulate air to meet cleanliness standards, regulate humidity, and maintain positive or negative pressure depending on the cleanroom’s needs. Effective HVAC design ensures that airborne contaminants are reduced, if not eliminated, and the internal environment stays within the specified limits of the cleanroom classification.
Cleanroom HVAC systems use high-efficiency particulate air (HEPA) or ultra-low particulate air (ULPA) filters to remove airborne particles. These filters can trap up to 99.99% of contaminants as small as 0.3 microns, ensuring the cleanroom meets ISO or GMP standards. Cleanrooms typically operate with laminar or turbulent airflow, which is created and controlled by the HVAC system to prevent particle buildup.
Maintaining appropriate pressure differentials between the cleanroom and adjacent areas is crucial to prevent contamination. Positive pressure is often used to keep contaminants out, while negative pressure may be used in areas dealing with hazardous materials. The HVAC system must ensure stable pressure gradients to prevent air from flowing in or out of the cleanroom inappropriately.
Many cleanroom processes are sensitive to temperature and humidity fluctuations, and even minor variations can impact product quality. HVAC systems in cleanrooms maintain precise temperature and humidity levels to prevent condensation, static buildup, and microbial growth, which could compromise the sterile environment. The control systems integrated with HVAC systems provide real-time monitoring to ensure consistency.
Proper airflow design is essential in cleanrooms to control contamination and maintain the desired cleanroom classification. Cleanrooms often utilize laminar flow, where air moves uniformly and at a constant speed to sweep away contaminants. In contrast, some areas may use turbulent flow for more flexible operations. The HVAC system must be carefully designed to control airflow patterns and ensure the air pressure and velocity match the room’s requirements.
Challenges in HVAC System Design for Cleanrooms
Designing an HVAC system for a cleanroom presents several challenges that must be carefully addressed to maintain performance and compliance.
Cleanroom HVAC systems often require 24/7 operation, making them energy-intensive. However, modern advancements such as energy-efficient filters, variable-speed drives, and heat recovery systems can significantly reduce energy costs.
Regular maintenance of HVAC systems is critical for sustained performance. Any lapse in maintenance can lead to a buildup of contaminants in filters, improper airflow, or fluctuating environmental conditions. Automated systems with real-time monitoring capabilities help maintain optimal performance and alert operators to necessary adjustments or repairs.
Cleanrooms must adhere to strict regulations such as ISO 14644, cGMP, or FDA guidelines. An HVAC system must be designed and maintained to ensure the cleanroom consistently meets these regulatory standards for cleanliness, temperature, humidity, and air pressure.
Importance of Redundancy and Backup Systems
In critical environments like pharmaceutical manufacturing or semiconductor production, even a brief HVAC system failure can lead to catastrophic contamination or product loss. Therefore, redundancy is vital in HVAC design for cleanrooms. Backup systems ensure continuous operation, and having multiple air handling units, backup power supplies, and automated control systems minimizes the risk of downtime.
The Future of Cleanroom HVAC Systems
Emerging technologies are pushing HVAC systems toward greater automation, real-time data analytics, and energy efficiency. Smart HVAC systems now integrate with building management systems (BMS) to monitor and adjust air quality, temperature, and pressure in real time. Energy-efficient solutions, such as variable frequency drives (VFDs) and advanced heat recovery systems, help reduce the operating costs of cleanroom HVAC systems, making them more sustainable.
Conclusion
HVAC systems in cleanrooms are indispensable for maintaining strict environmental controls. From air filtration and temperature regulation to pressure control, the HVAC system ensures that cleanrooms meet rigorous cleanliness and operational standards. Proper design, regular maintenance, and integration of advanced technologies are key to ensuring that cleanroom HVAC systems function optimally and in compliance with industry regulatio