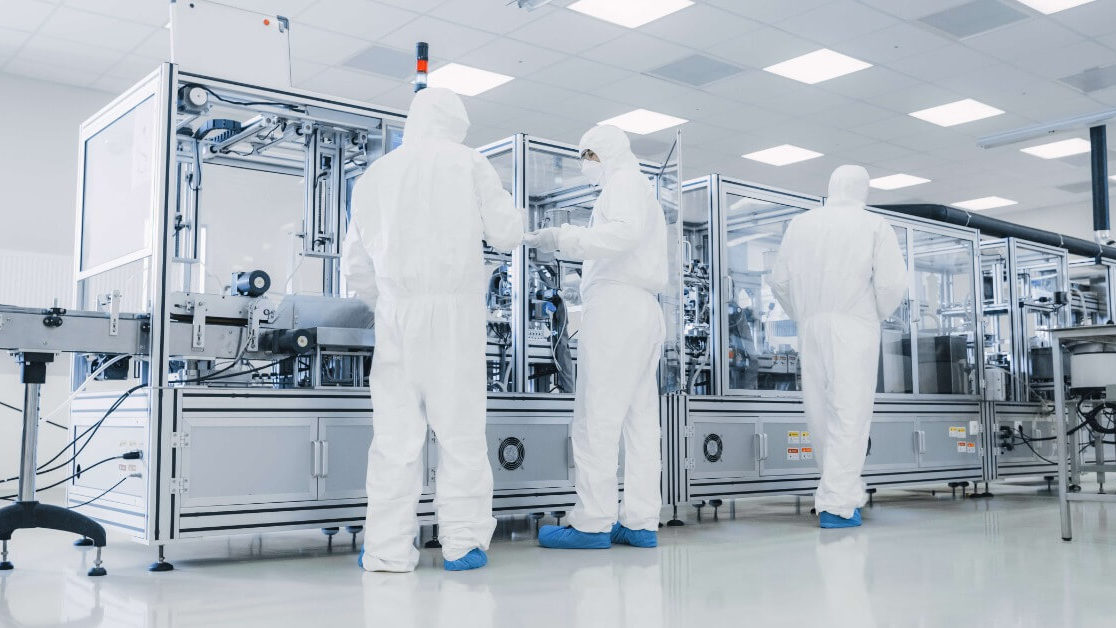
Piping Layout Considerations in Cleanrooms
When expanding a cleanroom, careful planning of the piping layout is crucial to maintaining the controlled environment’s operational efficiency, cleanliness, and compliance with standards like ISO 14644-1. An optimized piping layout can help reduce contamination risks, facilitate maintenance, and ensure that the expanded area integrates seamlessly with existing systems. Here are key factors to consider when optimizing the piping layout during cleanroom expansion.
Space Management and Flexibility
Cleanrooms are often designed to be modular or scalable, and piping layouts should support these design principles. As expansion occurs, the piping system must allow for:
- Efficient Use of Space – Piping should be routed in a way that maximizes floor and overhead space, avoiding interference with other critical systems like air handling units, electrical conduits, and cleanroom equipment.
- Adaptability for Future Expansions – Incorporating flexible piping systems that can easily accommodate future modifications is essential. Quick-disconnect fittings and flexible piping materials (such as stainless steel or Teflon) allow for easier reconfiguration without extensive downtime.
Minimizing Contamination Risk
Piping systems in cleanrooms, especially those for gases, water, and chemicals, must be designed with contamination control as a priority. Cleanroom piping layouts should:
- Reduce Turbulence – Avoid sharp bends and excessive angles, as these can cause turbulence, which increases the risk of particle generation and accumulation.
- Ensure Smooth Material Flow – Use appropriate piping materials (e.g., stainless steel, PVDF) that resist corrosion and contamination. These materials maintain the cleanliness of fluids and gases being transported throughout the facility.
- Position Piping Outside the Cleanroom Environment – Where possible, piping should be installed outside the cleanroom to reduce potential contamination sources. Penetrations into the cleanroom should be minimized and well-sealed.
Segregation of Systems
Different cleanroom processes may require separate piping systems, especially when dealing with highly sensitive materials or processes. Consider:
- Segregating High-Purity Systems – Piping for ultra-pure water (UPW), chemicals, or specialty gases should be completely segregated from systems that handle non-critical materials to prevent cross-contamination.
- Dedicated Lines for Critical Processes – Critical processes may require independent piping lines to ensure operational reliability and avoid contamination from other areas of the facility.
Efficient Routing and Maintenance Access
Piping layouts must balance operational efficiency with ease of access for routine inspections, cleaning, and maintenance:
- Group Pipes by Function – Routing pipes with similar functions (e.g., water, gases) in organized conduits or racks reduces clutter and ensures streamlined inspection or repair activities.
- Provide Accessible Maintenance Points – Access panels, shutoff valves, and monitoring points should be strategically placed to allow quick access during maintenance without disrupting the cleanroom’s operations.
Optimizing Energy Efficiency
As the cleanroom expands, energy consumption can increase significantly, particularly for systems involving HVAC and process piping. Energy-efficient designs are critical:
- Minimize Pressure Drops – Use larger pipe diameters or ensure smooth internal surfaces to reduce pressure drops and energy consumption in fluid and air transport systems.
- Insulate Piping – Proper insulation for hot or cold lines reduces energy loss and ensures the cleanroom’s temperature and humidity control systems work efficiently.
Coordination with HVAC and Utility Systems
Cleanroom expansions must ensure that the piping layout integrates smoothly with the HVAC system and other critical utilities:
- Ensure Proper Airflow Balance – The routing of piping systems, particularly for HVAC ducts, should not interfere with laminar airflow patterns in the cleanroom. This helps maintain air cleanliness and prevents particle contamination.
- Optimize Utility Piping Placement – Utility piping for gases, water, and waste should be designed to minimize overlap with critical air handling components.
Conclusion
An optimized piping layout is crucial to the success of any cleanroom expansion. By focusing on space management, contamination control, system segregation, and ease of maintenance, facility managers can ensure that the cleanroom operates efficiently and remains compliant with regulatory standards. Properly designed piping not only supports current operations but also allows for future scalability and minimizes operational disruptions during expansion.