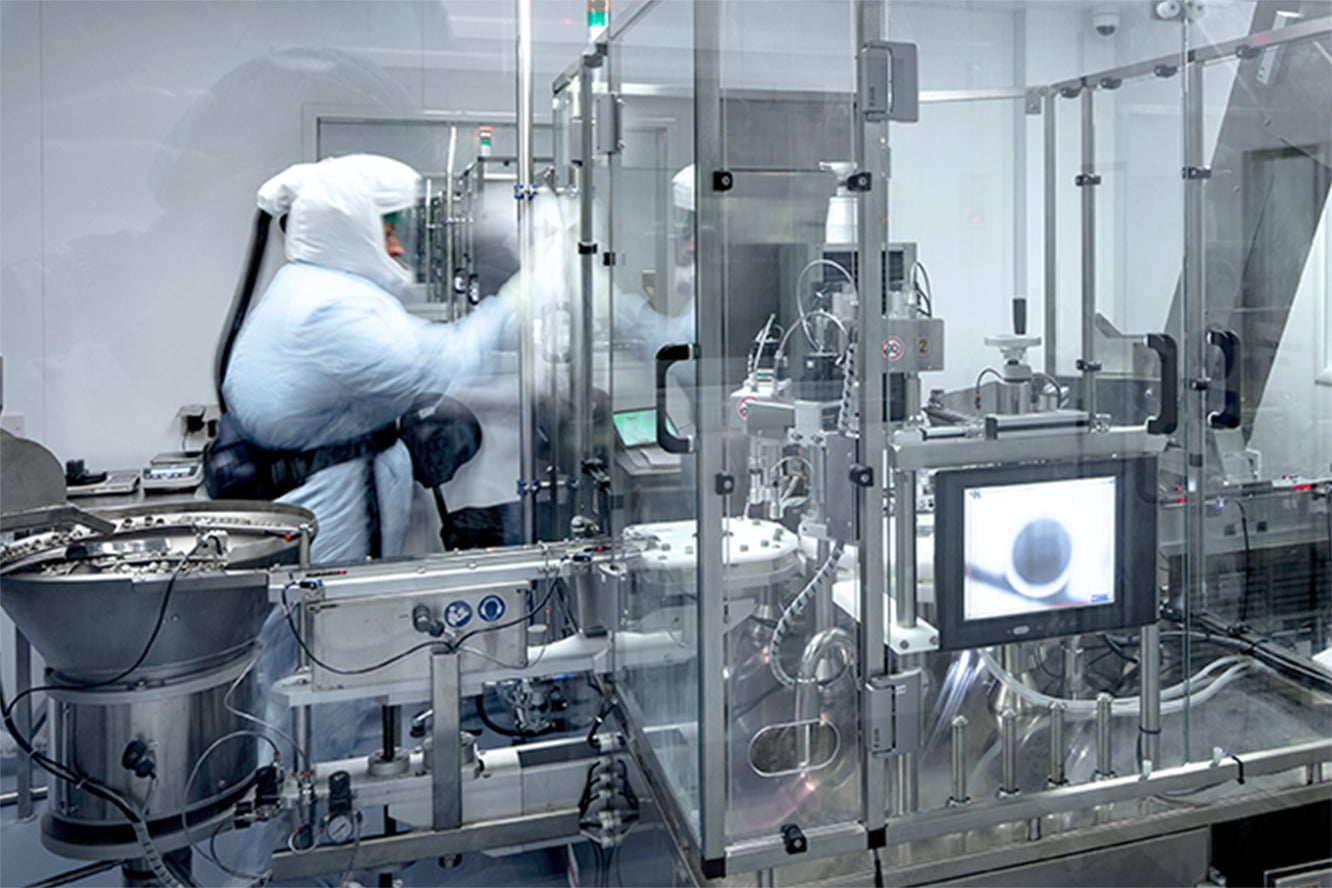
Piping and Ducting Integration with Cleanroom Filtration Systems
In a cleanroom environment, maintaining air purity and minimizing contamination is critical for industries like pharmaceuticals, semiconductors, and biotechnology. Piping and ducting systems are essential to delivering and distributing clean air, gases, and fluids while ensuring the cleanroom maintains its required standards for air quality. Proper integration of these systems with cleanroom filtration solutions enhances the overall performance and efficiency of the facility. Here’s a detailed breakdown of how piping and ducting integrate with filtration systems to optimize cleanroom operations.
Role of Piping and Ducting in Cleanroom Air Distribution
Cleanrooms depend heavily on their air distribution systems to maintain appropriate levels of cleanliness. Piping and ducting serve as the pathways for the movement of filtered air, gases, and other critical substances, such as purified water. These systems:
- Transport Filtered Air – Ducting is responsible for distributing filtered air from HVAC units to various zones within the cleanroom. It ensures that laminar airflow, critical for preventing contamination, is maintained.
- Deliver Gases and Fluids – Piping systems transport ultra-pure gases and fluids, which are vital for the cleanroom’s operations. The integration of piping with filtration systems ensures that contaminants in the air, gases, or fluids are eliminated before entering the cleanroom environment.
Air Filtration Systems and Ductwork Design
Ducting is typically connected to high-efficiency particulate air (HEPA) or ultra-low penetration air (ULPA) filters, which remove particles and contaminants from the air before it enters the cleanroom. Several key considerations apply when designing ductwork in conjunction with these filtration systems:
- Smooth Airflow – Ducts must be designed with minimal bends and restrictions to ensure that airflow remains laminar, reducing turbulence that could stir up particles.
- Airflow Balance – Integration of ducting with air filtration requires precise control of airflow rates, balancing positive and negative pressures within different cleanroom zones. This balance ensures contaminants are pushed out, rather than drawn in from less controlled areas.
- Contamination Prevention – Properly sealed ductwork prevents leaks or contamination from entering cleanroom spaces. Ducting materials must also be non-reactive and easily cleanable to maintain cleanliness standards.
Piping Systems and Gas Filtration
Piping used for cleanroom processes must meet stringent cleanliness and corrosion resistance standards. The gases and fluids transported through these systems must be filtered to remove any particulate, microbial, or chemical contaminants. Gas filtration involves:
- Point-of-Use Filtration – Filters are often installed at key points in the piping system to ensure that only pure, filtered gases are delivered to critical processes. These filters can be inline or incorporated into gas distribution manifolds.
- Use of High-Purity Materials – The choice of piping material, such as stainless steel or PVDF (polyvinylidene fluoride), ensures that the system remains free from contaminants. Corrosion-resistant materials help in maintaining gas purity over time.
Maintenance and Monitoring for Integrated Systems
The ongoing performance of both the filtration systems and the associated piping and ducting is essential for sustaining cleanroom operations. Integrated systems must be regularly maintained and monitored to prevent contamination and maintain air quality:
- Filter Replacement Schedules – Regular replacement of HEPA/ULPA filters is crucial to avoid pressure drops and maintain air cleanliness. Monitoring the pressure across filters can help identify when they need changing.
- Piping and Duct Cleaning – Regular cleaning and sterilization protocols are necessary for both piping and ducting systems. Specialized cleaning agents that do not introduce contaminants or residues into the cleanroom are used.
- Leak Detection – Integrated filtration and piping systems should include monitoring solutions that detect leaks or breaches, which could compromise cleanroom integrity.
Energy Efficiency in Integration
Integrating piping and ducting systems with filtration systems requires careful attention to energy efficiency. Air handling and filtration are among the highest energy-consuming components of cleanrooms. Optimizing these systems can significantly reduce operational costs while maintaining air quality:
- Optimized Airflow Designs – By designing ductwork to minimize pressure drops and maintaining proper insulation for piping, cleanrooms can operate more efficiently. The use of variable air volume (VAV) systems helps reduce energy consumption by adjusting airflow based on cleanroom demand.
- Energy-Efficient Filters – Selecting advanced filtration technologies, such as low-resistance HEPA filters, can also reduce the power requirements of the HVAC system while still maintaining required cleanliness levels.
Compliance with Cleanroom Standards
Both piping and ducting systems must comply with the ISO and GMP standards applicable to cleanrooms. Proper integration of these systems ensures the cleanroom maintains its classification and operates according to regulations:
- ISO 14644-1 – Ensures that both the air supply and the piped gases meet the required particulate standards for the cleanroom’s classification.
- GMP (Good Manufacturing Practices) – For cleanrooms used in pharmaceutical manufacturing, GMP standards require rigorous control over the piping and ducting systems to prevent cross-contamination and ensure product safety.
Conclusion
The integration of piping and ducting systems with cleanroom filtration is essential to maintaining air quality, controlling contamination, and optimizing cleanroom operations. By ensuring that these systems work in harmony, cleanroom facilities can meet stringent regulatory standards, provide a controlled environment for sensitive processes, and improve overall efficiency. Proper design, material selection, and ongoing maintenance are key to ensuring these systems remain effective in supporting the critical operations within a cleanroom.