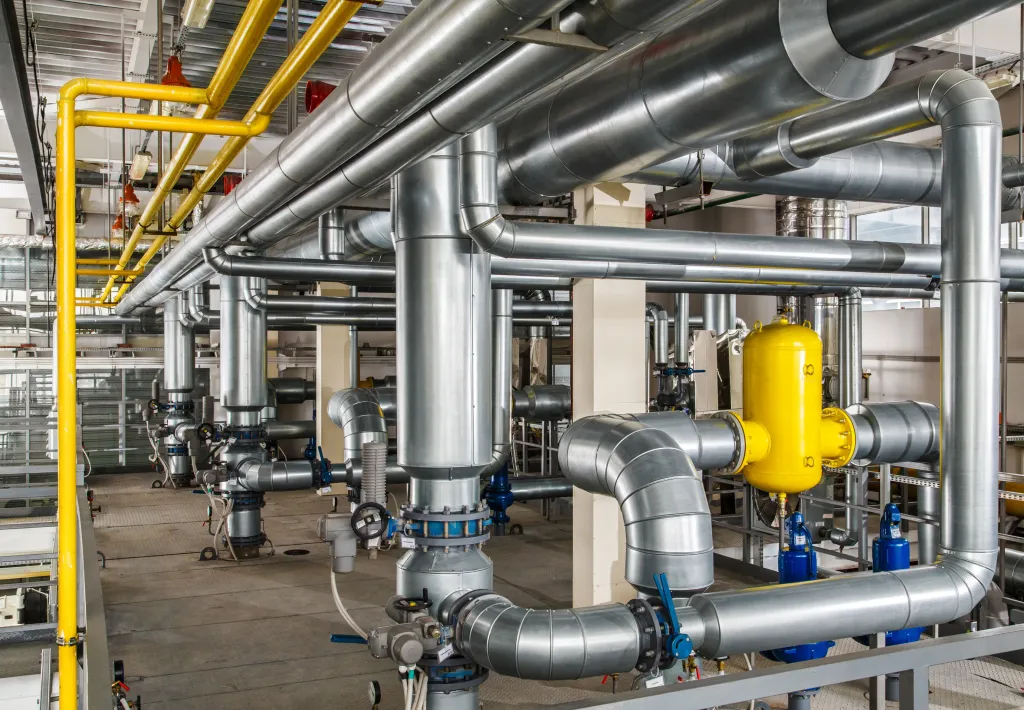
Piping Design Considerations in Cleanrooms
Designing an effective piping layout for cleanrooms requires careful consideration of cleanliness, contamination control, and the specific requirements of the cleanroom’s intended use. The goal is to ensure that the piping system supports the cleanroom’s environmental conditions while minimizing the risks of contamination. The design also needs to be adaptable to routine cleaning, maintenance, and operational efficiency.
Avoiding Contamination Risks
Controlling contamination is the main concern when designing piping layouts in cleanrooms. Contaminants such as particles, bacteria, and chemicals can easily accumulate in poorly designed systems. Piping systems should be designed with cleanliness in mind, focusing on the following factors:
- Minimizing Dead Legs – Dead legs are sections of piping where fluid becomes stagnant, leading to contamination buildup. Dead legs should be minimized or eliminated entirely in cleanroom piping designs, particularly in systems transporting purified water, process gases, or chemicals.
- Smooth Piping Surfaces – Piping materials with smooth, non-porous surfaces, such as stainless steel or specially treated polymers, should be used. This reduces the likelihood of particles or microorganisms adhering to the interior of the pipes.
- Using Sanitary Fittings – Fittings, valves, and connections are areas where contamination can occur. In cleanrooms, it is essential to use sanitary fittings that are easy to clean and designed to prevent contaminants from settling.
Fluid and Gas Distribution
Piping systems in cleanrooms often distribute fluids and gases to various equipment and workstations. The layout of these systems should be carefully planned to ensure an uninterrupted supply while preventing any potential cross-contamination.
- Dedicated Lines – It is important to use dedicated piping lines for different fluids and gases to avoid cross-contamination. For example, purified water lines should be separate from any chemical or gas lines.
- Loop Systems – Loop designs, where fluids are circulated continuously through the system, ensure consistent flow. These are particularly useful for systems distributing critical gases and liquids.
Ducting Systems
Ducting systems are essential for maintaining air quality and environmental control within cleanrooms. They are responsible for:
- Ventilation – Ensuring a consistent flow of filtered air to remove contaminants and maintain temperature and humidity levels.
- Air Filtration – Using HEPA (High-Efficiency Particulate Air) or ULPA (Ultra-Low Penetration Air) filters to capture airborne particles and microorganisms.
Piping Routes and Space Optimization
In cleanroom environments, space is often limited, and the piping layout must be optimized for both function and maintenance access. Piping routes should be planned to minimize disruptions to airflow and allow easy access for inspection or repair.
- Routing Through Ceilings and Walls – Piping is typically routed through the ceilings and walls to keep the cleanroom workspace free of obstructions. Overhead installations ensure that the piping does not interfere with personnel or equipment and reduce the risk of contamination from contact with pipes.
- Avoiding Bends and Restrictions – The layout should minimize unnecessary bends, restrictions, or sharp angles in the pipes, which can reduce flow efficiency and create points where contaminants may accumulate. Where bends are unavoidable, the radius of curvature should be large enough to allow smooth flow and easy cleaning.
Temperature Control and Insulation
Some fluids and gases used in cleanrooms need to be maintained at specific temperatures to ensure product quality or process integrity. For instance, purified water might need to remain at a certain temperature to prevent bacterial growth, while gases might need to be kept at stable pressures.
- Thermally Insulated Piping – Insulating the piping is crucial when dealing with temperature-sensitive fluids or gases. The insulation helps to maintain the desired temperature throughout the distribution system and prevents condensation, which can introduce moisture into the cleanroom environment.
- Heat Tracing – For systems that require more precise temperature control, heat tracing systems (either electrical or steam) can be applied to the pipes. These systems maintain the fluid’s temperature throughout the piping network, preventing unwanted fluctuations.
Cleaning and Maintenance
A well-designed piping layout should facilitate easy cleaning and maintenance. Cleanroom environments often require frequent cleaning and validation, and the piping system must be designed to accommodate these processes without introducing contamination risks or disrupting operations.
- Clean-in-Place (CIP) Systems – Many cleanroom piping systems are designed with Clean-in-Place (CIP) capabilities, allowing for the internal cleaning of pipes without disassembling the system. CIP systems typically circulate cleaning agents through the pipes and then flush them with sterile water.
- Drainage Systems – Proper drainage is essential to prevent any stagnant fluids from remaining in the system after cleaning. Piping should be designed with adequate slopes to ensure complete drainage.
Conclusion
Effective piping layout and design in cleanrooms are fundamental to ensuring both operational efficiency and contamination control. By carefully selecting materials, optimizing routing, ensuring cleanability, and maintaining compliance with industry standards, cleanroom facilities can uphold the highest levels of cleanliness and safety. Proper planning and execution in the design phase are crucial to minimizing long-term maintenance costs and contamination risks, ensuring a sustainable cleanroom environment.