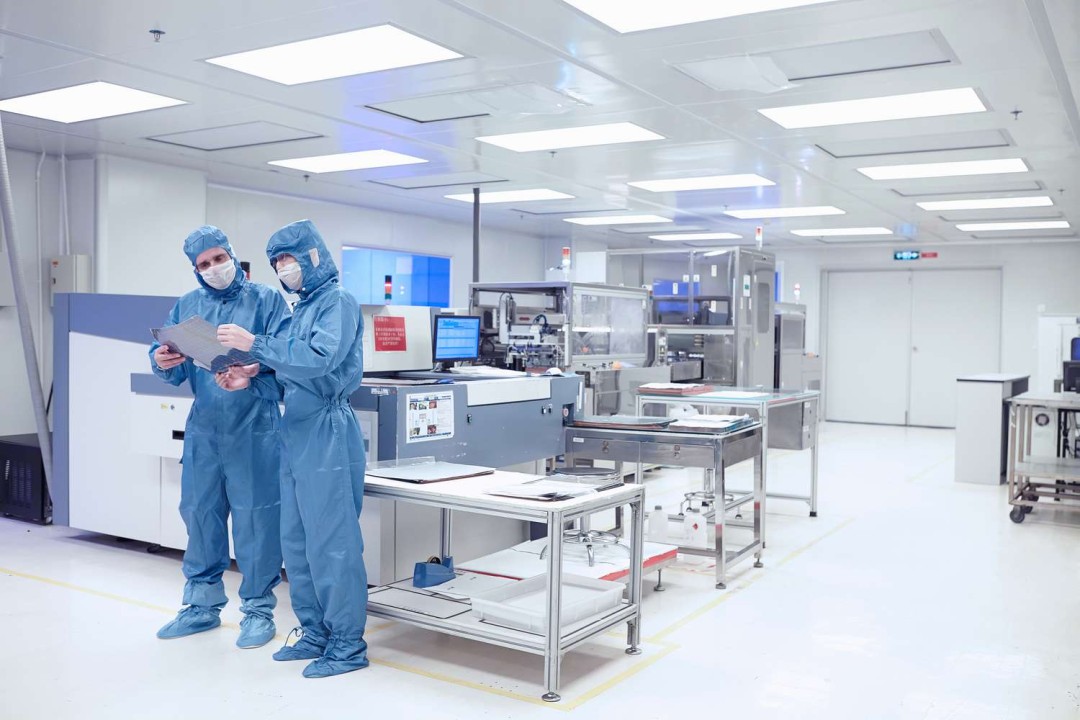
Respirators and Masks for Cleanroom Safety
Respirators and masks play a vital role in maintaining both worker safety and product integrity within cleanroom environments. Cleanrooms are controlled spaces where airborne contaminants must be kept to an absolute minimum, making respiratory protection essential for reducing particle contamination and safeguarding personnel from harmful substances. Properly selected and maintained respirators and masks form a critical barrier, protecting against both human-borne contaminants and environmental hazards.
Protecting Product Integrity
One of the primary purposes of masks in cleanrooms is to prevent human particles—such as skin flakes, hair, and saliva droplets—from contaminating sensitive products. Industries like pharmaceuticals, electronics, biotechnology, and aerospace require cleanroom workers to adhere to strict contamination control standards. Respirators and masks are essential in minimizing these human-borne contaminants, helping ensure product quality and preventing costly defects.
Cleanroom masks, often made from low-shedding materials, are designed to fit snugly around the mouth and nose to capture airborne particles from exhaled breath. This containment of particulates is especially crucial in ultra-clean environments, such as ISO Class 1 or 2 cleanrooms, where even the smallest contaminants can have significant impacts on production.
Ensuring Worker Safety
In addition to protecting products, respirators and masks are critical for worker safety, particularly in environments where hazardous chemicals, aerosols, or volatile organic compounds (VOCs) are present. Cleanrooms often contain chemical processes or involve the handling of nanoparticles that can be harmful if inhaled. In such cases, workers need respirators that filter out these harmful substances, ensuring their health is not compromised while performing tasks.
Respirators, such as N95 masks or powered air-purifying respirators (PAPRs), provide enhanced filtration, preventing workers from inhaling dangerous fumes, mists, or particles. These respirators are frequently used in cleanrooms where chemical processing or biohazard risks are high, ensuring a safe working environment.
Types of Respiratory Protection in Cleanrooms
These are typically used for environments where contamination control is necessary, but hazardous airborne particles are not present.
Widely used in cleanrooms with higher levels of airborne contamination risk, N95 respirators filter out 95% of airborne particles, providing a balance between protection and comfort. They are suitable for environments with potential chemical exposure or high particle risks.
These advanced respirators are equipped with a battery-operated blower that pushes filtered air into the mask. PAPRs are used in high-risk environments, such as those handling toxic chemicals or pathogens, where worker protection is paramount.
Compliance and Best Practices
Cleanroom respiratory protection must comply with strict standards, such as those set by the National Institute for Occupational Safety and Health (NIOSH) or the Occupational Safety and Health Administration (OSHA). Ensuring proper mask fit, regular maintenance, and adhering to replacement schedules is critical for effective contamination control and safety.
In addition, cleanroom workers must be trained on how to correctly wear and handle their respirators. Improper use can compromise both personal safety and cleanroom integrity, allowing contaminants to escape or harmful substances to penetrate.
Conclusion
Respirators and masks are an essential component of cleanroom safety, contributing to both product protection and worker well-being. Selecting the right type of respiratory protection based on the specific hazards and cleanliness requirements of the environment ensures compliance with industry standards and the overall success of cleanroom operations. Regular maintenance and training are key to maximizing the efficacy of respiratory protection in these controlled environments.