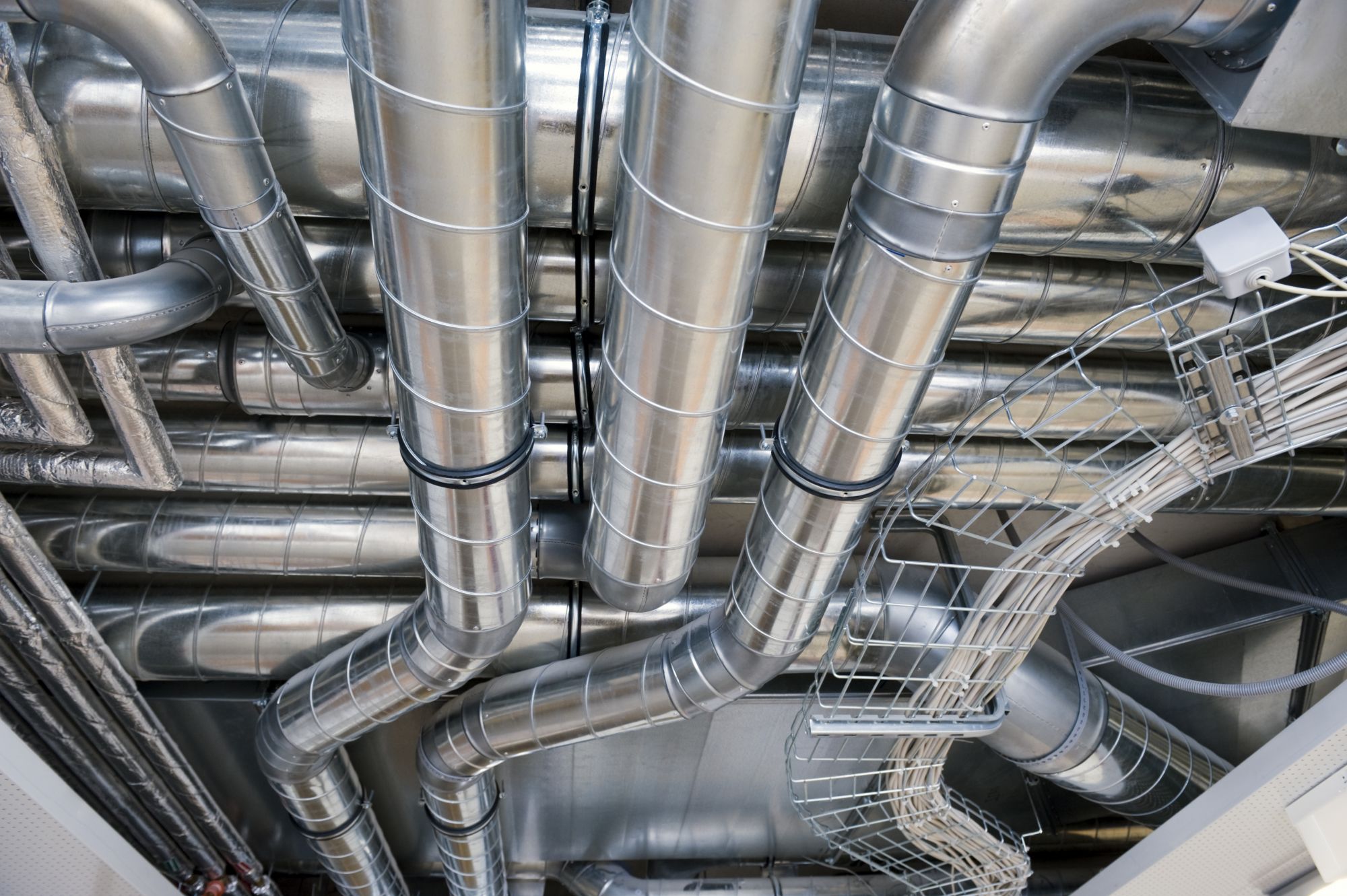
Solutions to Piping and Ducting Challenges in Cleanrooms
Piping and ducting systems, which are responsible for the transport of air, fluids, and gases, play a vital role in maintaining the cleanliness in cleanrooms. However, managing these systems can present several challenges, from contamination risks to material degradation, all of which can compromise the integrity of the cleanroom. Here’s a deeper look at some common challenges and practical solutions:
Contamination Risks in Piping and Ducting
- Challenge – Piping and ducting systems can become sources of contamination if not properly designed, installed, or maintained. Dust and debris can accumulate inside ducts and pipes, leading to compromised air or fluid quality.
- Solution – To mitigate contamination risks, cleanrooms use smooth, non-porous materials like stainless steel for pipes and ducts, which are easier to clean. Piping systems should be designed to minimize dead legs (sections where fluid can stagnate) and ensure smooth flow. Regular cleaning and sterilization procedures can prevent the buildup of residue inside piping.
Corrosion in Piping Systems
- Challenge – Corrosion is a major concern, particularly in systems that transport chemicals or high-purity water. Corroded pipes can lead to leaks and contamination. This could result in the release of particles into the cleanroom, affecting product quality.
- Solution – Using corrosion-resistant materials, such as stainless steel or chemically inert polymers helps prevent corrosion in piping systems. Regular inspections, coupled with proper material selection based on the type of fluids or gases being transported, can significantly reduce corrosion risk. Additionally, maintaining the correct pH and temperature of fluids reduces the likelihood of corrosion.
Pressure Leaks in Ducting and Piping
- Challenge – Pressure imbalances in ducting systems can lead to leaks or cracks, which allow contaminants to enter cleanroom environments. This is especially problematic in high-pressure systems or cleanrooms requiring strict positive or negative pressure conditions.
- Solution – Pressure testing and routine inspections are essential for identifying weak points in piping and ducting systems. Sealing leaks quickly with appropriate materials and ensuring that ductwork joints are properly secured and tested before installation are key preventive measures. Installing pressure sensors that monitor and alert for fluctuations can provide early detection of potential issues.
Inadequate Airflow in Ducting Systems
- Challenge – Improper airflow within ducting systems can lead to inefficient ventilation, affecting temperature control, humidity, and overall cleanroom air quality. Inadequate airflow also contributes to stagnant areas where contaminants can accumulate.
- Solution – Ductwork should be carefully designed to ensure laminar airflow (smooth, consistent flow with minimal turbulence), which is ideal for controlling particulate matter in cleanrooms. The use of HEPA or ULPA filters within the duct system ensures that airborne particles are filtered out before entering the cleanroom. Balancing airflow by incorporating adjustable dampers or using variable air volume (VAV) systems helps maintain consistent airflow patterns.
Cleaning and Maintenance Difficulties
- Challenge – Piping and ducting systems can be difficult to access for cleaning and maintenance, especially if they are installed in confined spaces or behind cleanroom walls. Over time, if these systems are not regularly cleaned, debris, chemical residues, and contaminants can accumulate.
- Solution – Designing systems with ease of maintenance in mind is important. This includes incorporating access points and inspection ports along pipes and ducts, which allow technicians to clean and inspect critical areas. For ducts, ensuring that filters and other components are easily replaceable can reduce downtime and cleaning difficulties.
Energy Efficiency and Operational Costs
- Challenge – Inefficient ducting and piping systems can lead to increased energy consumption, higher operational costs, and greater wear and tear on HVAC systems. Poorly designed ductwork can cause energy loss due to air leaks or require HVAC systems to work harder to maintain cleanroom conditions.
- Solution – Energy-efficient ducting and piping designs can help reduce operational costs. This includes using properly sized ducts, minimizing sharp bends, and ensuring tight sealing to prevent air leaks. Energy recovery systems can also be installed to recapture heat or cooling from exhaust air, reducing the load on HVAC systems. Regular maintenance to check for leaks and efficiency issues helps ensure optimal energy use.
Conclusion
By carefully selecting materials, designing for efficiency and ease of maintenance, and employing regular inspection and cleaning practices, cleanroom managers can reduce risks and improve overall system performance. These challenges and solutions not only ensure the longevity of the systems but also safeguard the integrity of the cleanroom itself, minimizing risks to product quality and safety.