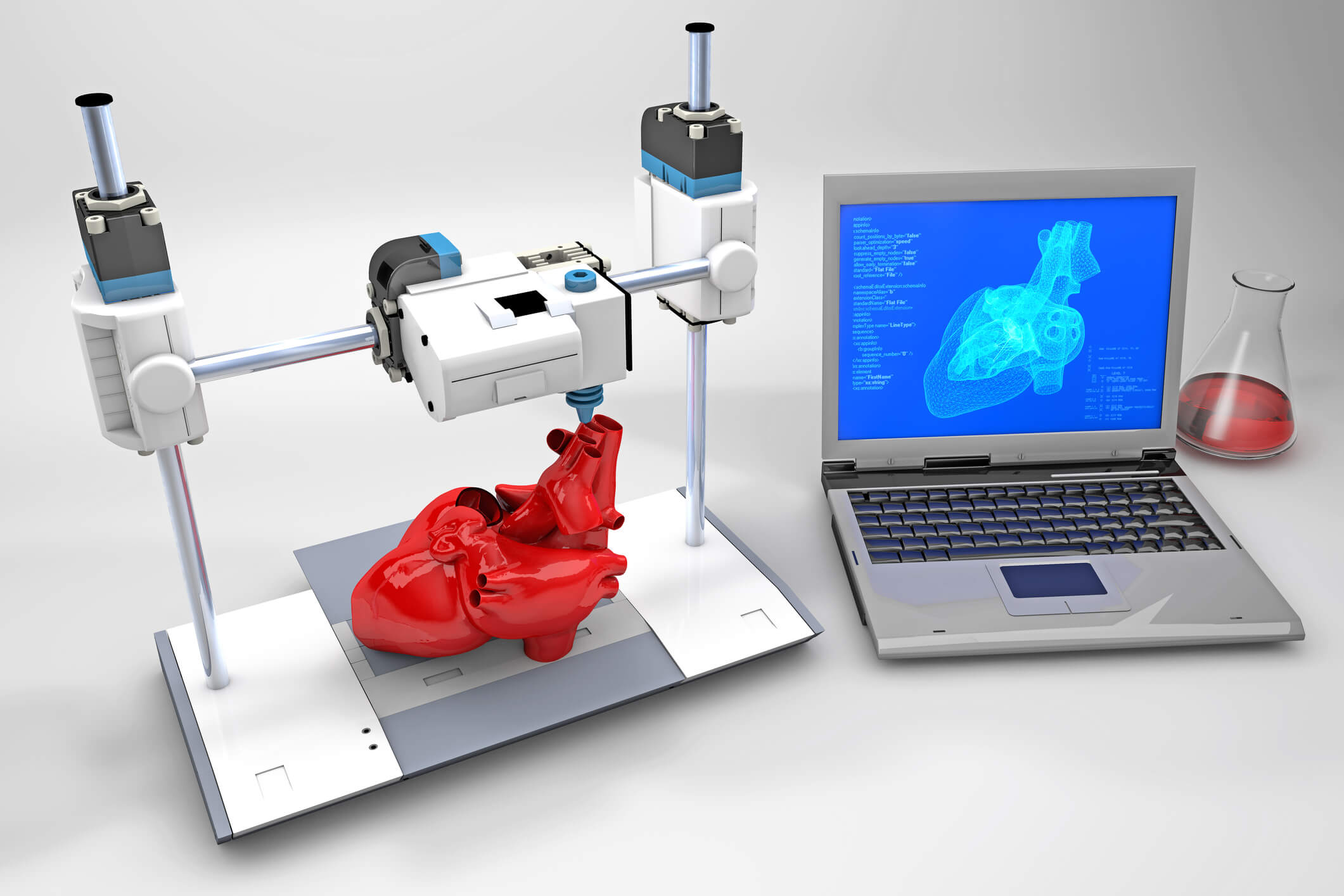
The Future of 3D Printing in Cleanrooms
The integration of 3D printing technology into cleanroom environments presents a transformative opportunity for industries that require stringent cleanliness standards, such as semiconductor manufacturing, pharmaceuticals, and biotechnology. This article explores the future of 3D printing in cleanrooms, highlighting both the opportunities it offers and the challenges that must be addressed.
Opportunities in 3D Printing for Cleanrooms
One of the most significant advantages of 3D printing is its potential to drastically reduce costs associated with manufacturing cleanroom equipment. Traditional cleanroom tools and components can be prohibitively expensive, often costing up to 90% more than their 3D printed counterparts. By utilizing additive manufacturing, laboratories can produce customized labware tailored to specific applications without incurring high costs. This capability allows for rapid prototyping and iteration, enabling researchers to quickly adapt tools to meet evolving project needs.
3D printing allows for the creation of complex geometries that are often impossible or cost-prohibitive with traditional manufacturing methods. This flexibility supports the development of bespoke equipment that can optimize workflows in cleanrooms. For instance, custom-designed wafer storage boxes and metrology tools have been successfully produced using various 3D printing materials, demonstrating that these printed items can perform comparably to commercial equivalents in terms of cleanliness and functionality.
The speed at which 3D printing can produce parts is another compelling advantage. With the ability to print on-demand, laboratories can significantly reduce lead times for obtaining necessary equipment. This rapid turnaround is especially beneficial in fast-paced research environments where time-sensitive experiments are common.
The use of 3D printing in cleanrooms also supports research and development efforts by enabling the creation of prototypes for testing new ideas quickly. Studies have shown that 3D printed objects can meet cleanliness standards required in semiconductor processing, with minimal particle generation during their use. This compatibility with cleanroom environments opens avenues for innovation across various scientific disciplines.
Challenges Facing 3D Printing in Cleanrooms
Despite the promising benefits, contamination remains a primary concern when integrating 3D printed components into cleanroom settings. The materials used in 3D printing must not only be compatible with the chemical processes involved but also generate minimal particles during their operation. Research indicates that while certain materials like polylactic acid (PLA) and acrylonitrile butadiene styrene (ABS) can produce parts that are comparable to traditional tools in terms of cleanliness, others like polypropylene (PP) may generate more particles.
The choice of materials is critical when considering 3D printing for cleanrooms. Not all filaments are suitable; those used must resist contamination from colorants and other additives. Studies recommend using natural-colored filaments to avoid metal impurities that could compromise sensitive processes. Additionally, the mechanical properties and chemical resistance of these materials must align with the rigorous demands of cleanroom applications.
Compliance with ISO standards is essential in cleanroom environments. The introduction of new materials or processes requires thorough testing to ensure they meet these stringent regulations. As such, ongoing research is necessary to validate the performance of new 3D printed components under controlled conditions.
The surface finish of 3D printed parts can pose challenges as well; layer lines from fused filament fabrication (FFF) processes may trap contaminants, complicating cleaning efforts. Effective post-processing techniques will be essential to ensure that printed components can be adequately cleaned and maintained within a cleanroom environment.
Conclusion
The future of 3D printing in cleanrooms is bright, characterized by significant opportunities for cost savings, customization, and enhanced efficiency. However, addressing challenges related to contamination risks, material limitations, regulatory compliance, and surface finish will be crucial for broader adoption. As research continues to validate the safety and efficacy of 3D printed components in these controlled environments, industries can expect a gradual shift towards integrating additive manufacturing as a standard practice within cleanrooms. This evolution will not only streamline operations but also foster innovation across various scientific fields.