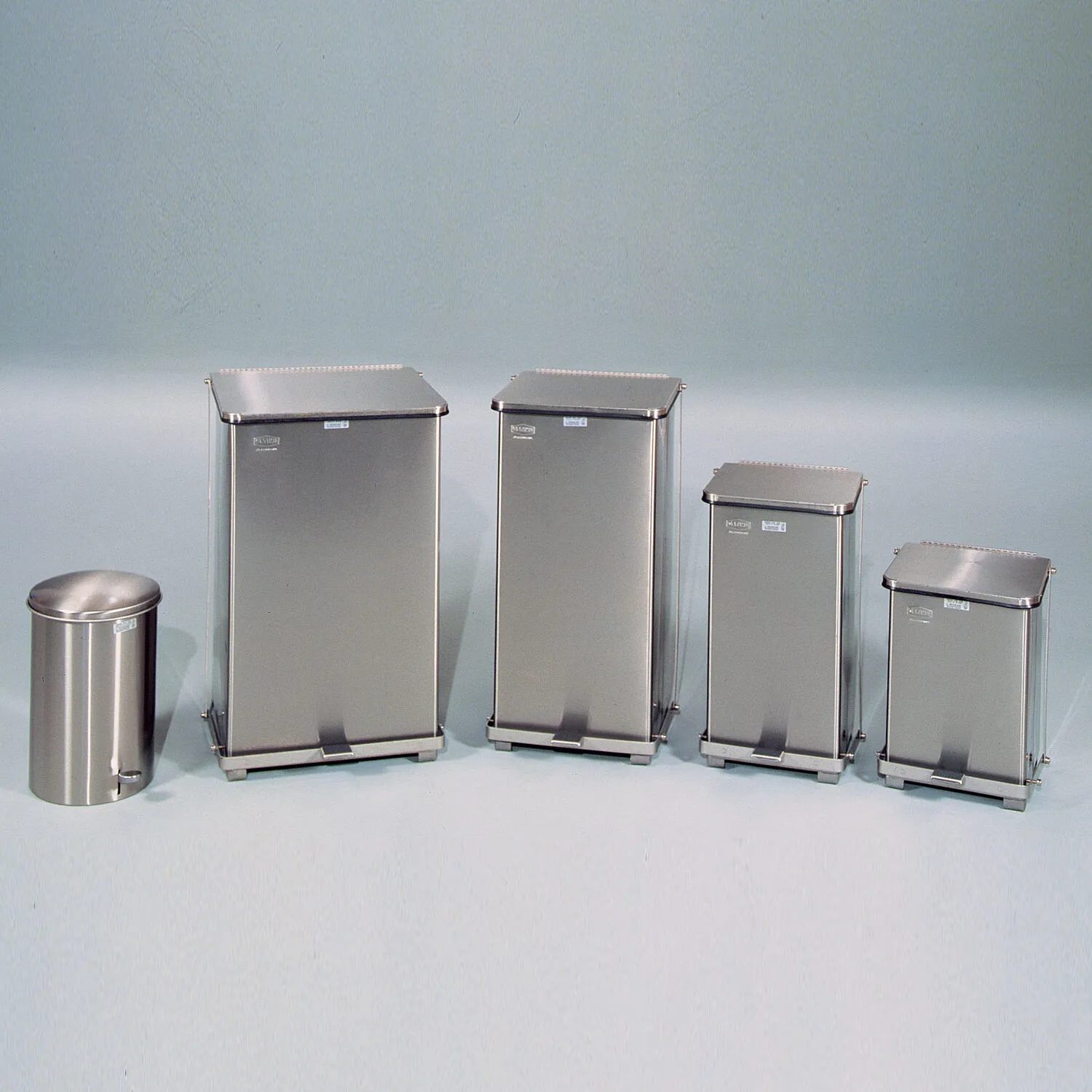
Waste Management in Cleanrooms
Effective waste management is key to maintaining a controlled and contamination-free environment. It is a complex and highly regulated process that requires careful planning and execution to maintain the sterile environment required in industries such as pharmaceuticals, biotechnology, and semiconductor manufacturing. By efficiently treating waste, we can ensure the cleanroom remains free of contamination, comply with environmental and safety standards, and support sustainability efforts.
Types of Waste in Cleanrooms
The type of waste produced in a cleanroom can differ significantly based on the industry and the particular purpose of the cleanroom. The first step in ensuring that materials are managed and disposed of according to their hazard classification is proper waste segregation.
General Waste
General waste in a cleanroom usually consists of non-contaminated materials generated from routine tasks like administrative duties, packaging, and product handling. While this waste doesn’t directly threaten contamination, it still needs to be managed with care to maintain the cleanroom’s sterile environment.
Packaging Materials – Cleanroom products often arrive in sealed packaging that may include plastic wraps, boxes, and other materials. These may not be contaminated, but they still need to be handled and disposed of in a way that avoids debris contamination.
Paper Products – Office-related materials such as used paper towels, writing pads, and printed reports.
Non-Contaminated PPE – Items like shoe covers, hairnets, and gloves that are clean when used but not contaminated during use.
Separation – General waste should be separated from contaminated waste at the source. This reduces the risk of cross-contamination.
Disposal – General waste is usually placed in cleanroom-approved waste bins that need to be covered and emptied on a regular basis to minimize contamination risks. In certain situations, general waste can be disposed of in standard waste streams, as long as it hasn’t been contaminated with hazardous materials.
Contaminated Waste
Contaminated waste includes materials that have been in contact with contaminants like dust, particulate matter, chemical residues, or biological agents, which can compromise the cleanroom’s environment. This type of waste carries a higher risk than general waste and must be handled with greater care.
PPE – Gloves, gowns, face masks, and shoe covers that have been worn in the cleanroom environment. These items may have come into contact with particulate matter, biological agents, or chemicals, thus potentially contaminating them.
Wipes & Cleaning Cloths – Wipes or cloths used for cleaning surfaces inside the cleanroom, which may be contaminated with particles or residues from products or processes.
Product Handling Materials – Items like trays, containers, or tools used to handle sensitive products that could have picked up contamination.
Containment – Contaminated waste must be placed in clearly marked, sealed containers to prevent the spread of contaminants. The containers should be puncture-resistant and leak-proof, and they should be properly labelled with information on the contents.
Storage – These materials should be stored in designated cleanroom waste areas until they are ready to be disposed of. The storage areas should be kept secure, clean, and regularly checked to ensure no waste spills or contamination.
Disposal – Depending on the level of contamination and the materials involved, contaminated waste may need to be treated (e.g., sterilization or decontamination) before it is sent for final disposal. Specialized disposal services for hazardous and biological waste may be required.
Hazardous Waste
Hazardous waste refers to substances that are harmful or toxic to human health or the environment. In cleanrooms, this type of waste can arise from the use of chemicals, biological agents, or materials involved in manufacturing processes, all of which can present serious risks if not handled properly.
PPE – Gloves, gowns, face masks, and shoe covers that have been worn in the cleanroom environment. These items may have come into contact with particulate matter, biological agents, or chemicals, thus potentially contaminating them.
Wipes & Cleaning Cloths – Wipes or cloths used for cleaning surfaces inside the cleanroom, which may be contaminated with particles or residues from products or processes.
Product Handling Materials – Items like trays, containers, or tools used to handle sensitive products that could have picked up contamination.
Segregation – Hazardous waste must be separated from non-hazardous waste to prevent accidental mixing. It should also be separated by category (e.g., chemical, biological) to avoid dangerous reactions.
Storage – Hazardous waste must be stored in specially designed containers that comply with legal and regulatory standards. These containers must be clearly labelled with the type of hazard (e.g., corrosive, toxic, flammable), and must be resistant to the waste material (e.g., corrosion-resistant for chemical waste).
Transportation and Disposal – Hazardous waste is usually handled by specialized disposal contractors. These professionals make sure that the waste is treated, neutralized, or disposed of safely in line with environmental regulations. For instance, certain chemicals might be neutralized at a chemical treatment facility, while biological waste often requires incineration or sterilization before disposal.
Waste Segregation
Effective waste segregation is crucial for a successful cleanroom waste management system. By categorizing waste into specific groups, cleanrooms can manage hazardous materials with utmost care, reducing the risk of contamination.
Purposes of Waste Segregation
- Prevent Cross-Contamination – Separation ensures that hazardous or contaminated materials do not come into contact with general waste or other cleanroom surfaces.
- Facilitate Proper Disposal – Different types of waste require different handling, storage, and disposal methods. Segregation ensures waste is being processed correctly.
- Enhance Safety – By segregating hazardous and non-hazardous materials, cleanroom staff are better protected from accidental exposure to harmful substances.
- Comply with Regulations – Local, national, and international regulations often mandate proper waste segregation as part of environmental and safety standards.
Key Practices in Waste Segregation
Waste should be sorted right at the source. For example, used gloves should be disposed of in a contaminated waste bin right after they are taken off, and general waste needs to be placed in placed in a separate bin from hazardous materials. This approach helps to minimize handling and lowers the chances of cross-contamination.
Use leak-proof hazardous waste containers that are resistant to the chemical or biological materials they contain. Use containers specifically designed for sharps and any waste that poses a risk of puncturing or cutting, like needles or broken glass. Make sure to use sealed biohazard bags that are intended for the safe containment of infectious materials.
Waste should not be stored in the cleanroom for extended periods. Removing waste frequently minimizes contamination risks and ensures that the waste does not disrupt operations.
Challenges in Waste Segregation
- Human Error – Improper segregation, such as mixing contaminated and general waste, can lead to contamination risks and increased disposal costs.
- Space Constraints – Smaller cleanrooms may struggle to allocate sufficient space for multiple waste bins or storage containers.
- Evolving Regulations – Regulations governing waste classification and segregation may change, requiring updates to policies and employee training.
Sustainability and Waste Reduction
Being sustainable and reducing waste are becoming increasingly important as industries strive to balance their operational needs with environmental responsibility. Cleanrooms inherently consume significant resources and generate waste, which makes it crucial to adopt sustainable practices to reduce their impact on the environment.
Sustainable Energy Use
Cleanrooms are energy-intensive due to the need for precise environmental controls. Reducing energy consumption contributes to sustainability.
- Energy-Efficient HVAC Systems – Upgrade to high-efficiency HEPA/ULPA filters and optimizing airflow patterns to reduce energy use. Install energy recovery ventilators (ERVs) to recycle energy from exhaust air. Implement variable frequency drives (VFDs) on HVAC motors to adjust airflow dynamically based on demand.
- Lighting Efficiency – Switch to LED lighting, which uses less energy and generates less heat, reducing the load on HVAC systems. Install motion-activated lighting systems to ensure lights are only on when areas are in use.
Innovative Technologies for Sustainability
Emerging technologies offer new opportunities for sustainable cleanroom operations.
- Smart Monitoring Systems – Using IoT (Internet of Things) sensors to monitor waste generation, energy consumption, and air quality in real time, enabling more targeted interventions.
- Advanced Filtration Systems – Filters that can be cleaned and reused, reducing the need for frequent replacement.
- Robotics and Automation – Automated waste handling systems that improve efficiency and reduce manual labor, minimizing contamination risks.
Conclusion
Managing waste in cleanrooms is crucial for keeping a controlled and contamination-free space. Proper practices for waste segregation, handling, disposal, and sustainability are necessary to ensure the cleanroom’s integrity and protect the environment. As industries shift towards greener practices, cleanroom waste management is also adapting, becoming more efficient and better aligned with sustainability goals.